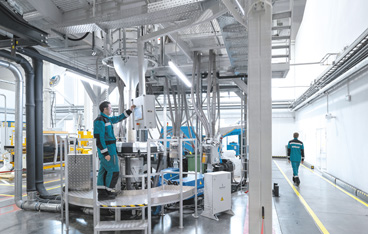
04.03.2024
Экструзия пленок с раздувом: неисправности оборудования
Специалисты R&D-центра «СИБУР ПолиЛаб» предлагают проанализировать проблемы, наиболее часто возникающие в процессе экструзии раздувных пленок на протяжении всего пути от засыпания гранул до намотки готовых рулонов, и посмотреть, как они связаны с состоянием основных узлов оборудования.
Износ шнека
Сердцем любой экструзионной линии является экструдер, а шнек — это неотъемлемая часть экструдера. Но важно понимать, что ни один шнек не может работать вечно, поэтому можно сказать, что шнек является таким же расходным материалом, как, например, резиновая прокладка или подшипник.
По статистике начало износа шнека при работе линии в режиме 24×7 и 365 дней в году приходится на промежуток от 2 до 5 лет. При этом использование абразивных добавок (например, TiO2 или CaCO3) в рецептурах может ускорить изнашивание этой запчасти. Индикаторами износа шнека могут являться такие проблемы, как повышение температуры расплава; пульсация материала, которая выражается в волнообразных изменениях давления расплава и нагрузки на привод; повышенный уровень деструкции полимеров при выходе расплава из фильеры (нагары); усиленное гелеобразование.
Многие производители оборудования и поставщики сырья рекомендуют использовать полезный инструмент самоконтроля — оценку удельного выхода расплава. Что это такое? При переработке определенной марки сырья (зачастую это наиболее используемая марка и желательно одной партии) необходимо оценивать объем выхода расплава за единицу времени при фиксированной скорости вращения шнека. Данную процедуру контроля технического состояния рекомендуется выполнять каждые полгода, максимум — каждый год. Разброс между результатами удельного выхода должен быть сопоставим с погрешностью дозатора. Если же разброс между измерениями за 2-3 временных отрезка превышает погрешность дозатора, то это повод задуматься о состоянии шнека.
Также помимо оценки удельного выхода можно применять другой подход: полное извлечение шнека с последующим измерением диаметра витков. Но данный метод требует большей затраты времени и усилий.
Забивка системы охлаждения зоны питания шнека
Каналы системы охлаждения зоны питания шнека могут забиваться по следующим причинам:
— загрязнение воды или ее повышенная минерализация, приводящая к образованию минеральных отложений;
— недостаточный напор воды. Если цех переработчика спроектирован для установки, к примеру, только трех экструзионных линий, то после монтажа и запуска четвертой возможно возникновение проблем как на новой линии, так и на старых. Причина кроется в том, что системе водоснабжения в принципе не хватает воды.
Забивка системы охлаждения может привести к неприятным последствиям.
Во-первых, к повышению температуры в зоне питания шнека (более 50°С), что может стать причиной волнообразного изменения давления расплава и, как следствие, разнотолщинности в продольном направлении.
Во-вторых, к возникновению непроплавов на пленочном полотне.
Рекомендация специалистов в данном случае: не пренебрегать техническими требованиями производителей оборудования в отношении проектирования системы водоснабжения и обращать внимание на качество воды. Например, в центре «СИБУР ПолиЛаб» проводится ежемесячный контроль характеристик воды в сторонней лаборатории. В случае отклонений во внутренний контур системы водноснабжения добавляются концентраты растворов с модифицирующими компонентами — pH-буферами или коагулянтами.
Также необходимо периодически осуществлять осмотр узлов подвода воды к зонам охлаждения и осуществлять их профилактическую чистку.
Неисправность двигателя и привода экструдера
Следующие потенциально проблемные узлы экструдера — двигатель и привод. Их неисправность может вызывать ряд неприятных проблем, таких как перегрузки, скачкообразные изменения нагрузки на двигатель и изменения скорости вращения шнека. Периодическое техническое обслуживание может помочь избежать подобных ситуаций.
Поломка нагревательных элементов
Причиной возможных проблем, возникающих в процессе экструзии, может являться поломка нагревательных элементов, которые могут перегревать зоны экструдера-фильеры или недостаточно нагревать их.
Проблемы с нагревательными элементами влияют на стабильность как переработки, так и потока расплава, пузыря, давления и гомогенизации расплава. Неисправность нагревателя даже в одной зоне может вызвать усиленное гелеобразование. Удобным инструментом выявления поломок нагревательных элементов является периодический мониторинг силы тока на каждом нагревательном элементе.
Некорректность работы контроллеров питания и термопар по сути связаны с выше описанным дефектом, ведь если контроллер и термопара неисправны, то управляющий компьютер линии считает, что зона всегда недостаточно нагрета и продолжает ее нагревать, что в свою очередь может привести к самым негативным последствиям вплоть до возгорания.
Деструкция материала внутри каналов фильеры
Термодеструкцию полимеров внутри фильеры практически невозможно предотвратить, но при правильной эксплуатации линии можно добиться снижения частоты вынужденных остановок для чистки.
Продукты деструкции полимера могут время от времени выходить на поверхности пленки. Деструктированный полимер в каналах фильеры и на самой кромке может вызывать появление полос на пленочном полотне в продольном направлении.
Как с этим бороться? Для митигации (смягчения последствий) загрязнений помогает своевременная прочистка экструдеров и фильеры. Если эта мера уже не помогает, то необходимо осуществить разбор фильеры с полным извлечением спиралей фильеры и прочистить их механически с использованием латунных инструментов и специальных чистящих паст.
Следует помнить, что правильный порядок остановки экструзионной линии позволяет минимизировать риск образования нагара.
Остановку линии желательно проводить при переработке высоковязкого ПЭНП или ПЭВП (возможно, с добавлением концентратов антиоксидантов) в момент максимального охлаждения экструдера и температуре смеси 180°С. По мере охлаждения линии необходимо уменьшать скорость вращения шнека, чтобы зоны экструдера не разогревались ввиду возникновения силы трения. После полной остановки экструзии расплав из зазора фильеры вычищать не нужно, наоборот, важно максимально плотно закрыть зазор фильеры для исключения попадания воздуха. Эта мера позволит минимизировать термодеструкцию.
Отложения на фильере
Отложения на фильере (die build-up) — частный случай нагарообразования, который также влияет на внешний вид пленки (появляются полосы в продольном направлении) и ее разнотолщинность. Деструкция полимера на краях фильеры протекает гораздо быстрее из-за контакта горячего полимера с воздухом.
Что нужно предпринимать, чтобы минимизировать образование нагаров?
Зазор фильеры необходимо качественно зачищать перед каждым пуском линии. Следует наносить силиконовую смазку на края фильеры при пуске. Необходимо контролировать температуры экструзии, использовать только рекомендованные температурные режимы. Применение процессинговых добавок может существенно уменьшить количество отложений на фильере. Иногда несоответствие конфигурации экструдера и перерабатываемого сырья может приводить к появлению нагара.
После процедуры чистки фильеры следует обязательно проверить корректность выставленного зазора.
Неоткалиброванный зазор фильеры
Еще одной, возможно, не самой очевидной проблемой в работе оборудования, которая, однако, сказывается и на внешнем виде, и на свойствах пленок, является некорректно откалиброванный зазор фильеры. Именно он становится одной из ключевых причин разнотолщинности пленки. Отклонения от горизонтальной линии кристаллизации приводит к неравномерности вытяжки расплава и его охлаждения, что приводит к ухудшению физико-механических параметров и оптических характеристик пленок.
Чистота узлов IBC
Процедура, которую иногда неоправданно игнорируют, — это поддержание в чистоте системы воздушного охлаждения пленочного пузыря (Internal Bubble Cooling — IBC). Важно понимать, что продукты деструкции полимеров и функциональных добавок (мастербатчей) постоянно откладываются на узлах IBC и самом воздушном кольце. Расплав при соприкосновении с микрофрагментами парафинов и масел может образовывать дефект на поверхности пленки — «линза».
Отложения на отверстиях воздуховодов могут влиять на равномерность воздушного потока, который охлаждает пузырь или его раздувает/сдувает, что впоследствии сказывается на стабильности пузыря и качественном его охлаждении. Производитель пленок должен в обязательном порядке проводить плановую чистку всех узлов системы воздушного охлаждения.
Контроль натяжения и складки
на пленочном полотне
Проблемы могут возникать и на этапах вытяжки и намотки пленок. Если на пленочном полотне после складывающей рамы образуются складки, то необходимо рассмотреть следующие причины появления данного рода дефектов:
— слишком высокое натяжение пленки между узлом стягивателя и складывающей рамой. Для каждого типа пленки необходимо эмпирически подбирать такие настройки;
— неисправность тензодатчиков или контроллеров натяжения стягивателя. Это стоит проверить, если очевидно, что уже подобранные вытяжные режимы перестали работать для определенного вида пленки;
— повреждения или износ вытяжных валов, которые также могут вызывать неоднородности в натяжении полотна пленки.
Морщинистость пленки после схлопывающей рамы
Морщинистость пленки после складывающей рамы может проявляться вследствие следующих причин:
— слишком малый угол складывающей рамы, который может привести к образованию морщин по центру пленочного полотна;
— слишком большой угол складывающей рамы. Приведет к появлению морщин на краях полотна;
— заклинивание вытягивающих роликов на складывающей раме. Зачастую для решения этой проблемы достаточно провести дефектовку подшипников и произвести их замену;
— некорректно выставленная стабилизирующая корзина. Пузырь не должен упираться в валики корзины, необходимо лишь легкое его касание.
Отдельно стоит отметить, что наличие воздуха в пленочном рукаве после схлопывающей рамы является критически важным для дальнейшего ровного скольжения рукава до узла намотки, поэтому после пуска линии и выхода на мастер-режим необходимо уделить особое внимание данной проблеме. Если операторы уверены, что прижимное давление достаточно и проблем с положением валов и их состоянием нет, то необходимо подняться на самый верхний ярус линии и после вытяжных валов произвести несколько надрезов пленочного рукава в местах скопления воздуха, а через несколько минут убедиться в отсутствии воздушных пузырей в сложенном рукаве.
Конусность намотки пленки
Плохое качество намотки пленки наиболее часто выражается в виде конусности рулона. Одна из причин неравномерной намотки — разнотолщинность и отсутствие осцилляции. Для решения данной проблемы необходимо вернуться чуть назад и устранить причины разнотолщинности, и/или включить и настроить режим осцилляции.
Тупые ножи также могут влиять на процесс резки пленки необходимого формата. Если есть даже небольшое коробление торца резанной пленки, то на рулоне большого диаметра это может привести к дефекту.
Слабое натяжение полотна на намотчике также может быть причиной конусности намотки. В таком случае необходимо подобрать оптимальный режим натяжения пленки на намотчике.
Описанные выше проблемы — лишь часть возможных проблем и трудностей, с которыми может столкнуться переработчик. И каждая из них должна рассматриваться комплексно, поэтому специалисты «СИБУР ПолиЛаб» приглашают заинтересованных слушателей на специальный вебинар, посвященный данной тематике и проводимый на платформе «Бизнес-практики «СИБУР», во время которого можно задать вопросы и получить индивидуальную консультацию.
Посмотреть в журнале
Износ шнека
Сердцем любой экструзионной линии является экструдер, а шнек — это неотъемлемая часть экструдера. Но важно понимать, что ни один шнек не может работать вечно, поэтому можно сказать, что шнек является таким же расходным материалом, как, например, резиновая прокладка или подшипник.
По статистике начало износа шнека при работе линии в режиме 24×7 и 365 дней в году приходится на промежуток от 2 до 5 лет. При этом использование абразивных добавок (например, TiO2 или CaCO3) в рецептурах может ускорить изнашивание этой запчасти. Индикаторами износа шнека могут являться такие проблемы, как повышение температуры расплава; пульсация материала, которая выражается в волнообразных изменениях давления расплава и нагрузки на привод; повышенный уровень деструкции полимеров при выходе расплава из фильеры (нагары); усиленное гелеобразование.
Многие производители оборудования и поставщики сырья рекомендуют использовать полезный инструмент самоконтроля — оценку удельного выхода расплава. Что это такое? При переработке определенной марки сырья (зачастую это наиболее используемая марка и желательно одной партии) необходимо оценивать объем выхода расплава за единицу времени при фиксированной скорости вращения шнека. Данную процедуру контроля технического состояния рекомендуется выполнять каждые полгода, максимум — каждый год. Разброс между результатами удельного выхода должен быть сопоставим с погрешностью дозатора. Если же разброс между измерениями за 2-3 временных отрезка превышает погрешность дозатора, то это повод задуматься о состоянии шнека.
Также помимо оценки удельного выхода можно применять другой подход: полное извлечение шнека с последующим измерением диаметра витков. Но данный метод требует большей затраты времени и усилий.
Забивка системы охлаждения зоны питания шнека
Каналы системы охлаждения зоны питания шнека могут забиваться по следующим причинам:
— загрязнение воды или ее повышенная минерализация, приводящая к образованию минеральных отложений;
— недостаточный напор воды. Если цех переработчика спроектирован для установки, к примеру, только трех экструзионных линий, то после монтажа и запуска четвертой возможно возникновение проблем как на новой линии, так и на старых. Причина кроется в том, что системе водоснабжения в принципе не хватает воды.
Забивка системы охлаждения может привести к неприятным последствиям.
Во-первых, к повышению температуры в зоне питания шнека (более 50°С), что может стать причиной волнообразного изменения давления расплава и, как следствие, разнотолщинности в продольном направлении.
Во-вторых, к возникновению непроплавов на пленочном полотне.
Рекомендация специалистов в данном случае: не пренебрегать техническими требованиями производителей оборудования в отношении проектирования системы водоснабжения и обращать внимание на качество воды. Например, в центре «СИБУР ПолиЛаб» проводится ежемесячный контроль характеристик воды в сторонней лаборатории. В случае отклонений во внутренний контур системы водноснабжения добавляются концентраты растворов с модифицирующими компонентами — pH-буферами или коагулянтами.
Также необходимо периодически осуществлять осмотр узлов подвода воды к зонам охлаждения и осуществлять их профилактическую чистку.
Неисправность двигателя и привода экструдера
Следующие потенциально проблемные узлы экструдера — двигатель и привод. Их неисправность может вызывать ряд неприятных проблем, таких как перегрузки, скачкообразные изменения нагрузки на двигатель и изменения скорости вращения шнека. Периодическое техническое обслуживание может помочь избежать подобных ситуаций.
Поломка нагревательных элементов
Причиной возможных проблем, возникающих в процессе экструзии, может являться поломка нагревательных элементов, которые могут перегревать зоны экструдера-фильеры или недостаточно нагревать их.
Проблемы с нагревательными элементами влияют на стабильность как переработки, так и потока расплава, пузыря, давления и гомогенизации расплава. Неисправность нагревателя даже в одной зоне может вызвать усиленное гелеобразование. Удобным инструментом выявления поломок нагревательных элементов является периодический мониторинг силы тока на каждом нагревательном элементе.
Некорректность работы контроллеров питания и термопар по сути связаны с выше описанным дефектом, ведь если контроллер и термопара неисправны, то управляющий компьютер линии считает, что зона всегда недостаточно нагрета и продолжает ее нагревать, что в свою очередь может привести к самым негативным последствиям вплоть до возгорания.
Деструкция материала внутри каналов фильеры
Термодеструкцию полимеров внутри фильеры практически невозможно предотвратить, но при правильной эксплуатации линии можно добиться снижения частоты вынужденных остановок для чистки.
Продукты деструкции полимера могут время от времени выходить на поверхности пленки. Деструктированный полимер в каналах фильеры и на самой кромке может вызывать появление полос на пленочном полотне в продольном направлении.
Как с этим бороться? Для митигации (смягчения последствий) загрязнений помогает своевременная прочистка экструдеров и фильеры. Если эта мера уже не помогает, то необходимо осуществить разбор фильеры с полным извлечением спиралей фильеры и прочистить их механически с использованием латунных инструментов и специальных чистящих паст.
Следует помнить, что правильный порядок остановки экструзионной линии позволяет минимизировать риск образования нагара.
Остановку линии желательно проводить при переработке высоковязкого ПЭНП или ПЭВП (возможно, с добавлением концентратов антиоксидантов) в момент максимального охлаждения экструдера и температуре смеси 180°С. По мере охлаждения линии необходимо уменьшать скорость вращения шнека, чтобы зоны экструдера не разогревались ввиду возникновения силы трения. После полной остановки экструзии расплав из зазора фильеры вычищать не нужно, наоборот, важно максимально плотно закрыть зазор фильеры для исключения попадания воздуха. Эта мера позволит минимизировать термодеструкцию.
Отложения на фильере
Отложения на фильере (die build-up) — частный случай нагарообразования, который также влияет на внешний вид пленки (появляются полосы в продольном направлении) и ее разнотолщинность. Деструкция полимера на краях фильеры протекает гораздо быстрее из-за контакта горячего полимера с воздухом.
Что нужно предпринимать, чтобы минимизировать образование нагаров?
Зазор фильеры необходимо качественно зачищать перед каждым пуском линии. Следует наносить силиконовую смазку на края фильеры при пуске. Необходимо контролировать температуры экструзии, использовать только рекомендованные температурные режимы. Применение процессинговых добавок может существенно уменьшить количество отложений на фильере. Иногда несоответствие конфигурации экструдера и перерабатываемого сырья может приводить к появлению нагара.
После процедуры чистки фильеры следует обязательно проверить корректность выставленного зазора.
Неоткалиброванный зазор фильеры
Еще одной, возможно, не самой очевидной проблемой в работе оборудования, которая, однако, сказывается и на внешнем виде, и на свойствах пленок, является некорректно откалиброванный зазор фильеры. Именно он становится одной из ключевых причин разнотолщинности пленки. Отклонения от горизонтальной линии кристаллизации приводит к неравномерности вытяжки расплава и его охлаждения, что приводит к ухудшению физико-механических параметров и оптических характеристик пленок.
Чистота узлов IBC
Процедура, которую иногда неоправданно игнорируют, — это поддержание в чистоте системы воздушного охлаждения пленочного пузыря (Internal Bubble Cooling — IBC). Важно понимать, что продукты деструкции полимеров и функциональных добавок (мастербатчей) постоянно откладываются на узлах IBC и самом воздушном кольце. Расплав при соприкосновении с микрофрагментами парафинов и масел может образовывать дефект на поверхности пленки — «линза».
Отложения на отверстиях воздуховодов могут влиять на равномерность воздушного потока, который охлаждает пузырь или его раздувает/сдувает, что впоследствии сказывается на стабильности пузыря и качественном его охлаждении. Производитель пленок должен в обязательном порядке проводить плановую чистку всех узлов системы воздушного охлаждения.
Контроль натяжения и складки
на пленочном полотне
Проблемы могут возникать и на этапах вытяжки и намотки пленок. Если на пленочном полотне после складывающей рамы образуются складки, то необходимо рассмотреть следующие причины появления данного рода дефектов:
— слишком высокое натяжение пленки между узлом стягивателя и складывающей рамой. Для каждого типа пленки необходимо эмпирически подбирать такие настройки;
— неисправность тензодатчиков или контроллеров натяжения стягивателя. Это стоит проверить, если очевидно, что уже подобранные вытяжные режимы перестали работать для определенного вида пленки;
— повреждения или износ вытяжных валов, которые также могут вызывать неоднородности в натяжении полотна пленки.
Морщинистость пленки после схлопывающей рамы
Морщинистость пленки после складывающей рамы может проявляться вследствие следующих причин:
— слишком малый угол складывающей рамы, который может привести к образованию морщин по центру пленочного полотна;
— слишком большой угол складывающей рамы. Приведет к появлению морщин на краях полотна;
— заклинивание вытягивающих роликов на складывающей раме. Зачастую для решения этой проблемы достаточно провести дефектовку подшипников и произвести их замену;
— некорректно выставленная стабилизирующая корзина. Пузырь не должен упираться в валики корзины, необходимо лишь легкое его касание.
Отдельно стоит отметить, что наличие воздуха в пленочном рукаве после схлопывающей рамы является критически важным для дальнейшего ровного скольжения рукава до узла намотки, поэтому после пуска линии и выхода на мастер-режим необходимо уделить особое внимание данной проблеме. Если операторы уверены, что прижимное давление достаточно и проблем с положением валов и их состоянием нет, то необходимо подняться на самый верхний ярус линии и после вытяжных валов произвести несколько надрезов пленочного рукава в местах скопления воздуха, а через несколько минут убедиться в отсутствии воздушных пузырей в сложенном рукаве.
Конусность намотки пленки
Плохое качество намотки пленки наиболее часто выражается в виде конусности рулона. Одна из причин неравномерной намотки — разнотолщинность и отсутствие осцилляции. Для решения данной проблемы необходимо вернуться чуть назад и устранить причины разнотолщинности, и/или включить и настроить режим осцилляции.
Тупые ножи также могут влиять на процесс резки пленки необходимого формата. Если есть даже небольшое коробление торца резанной пленки, то на рулоне большого диаметра это может привести к дефекту.
Слабое натяжение полотна на намотчике также может быть причиной конусности намотки. В таком случае необходимо подобрать оптимальный режим натяжения пленки на намотчике.
Описанные выше проблемы — лишь часть возможных проблем и трудностей, с которыми может столкнуться переработчик. И каждая из них должна рассматриваться комплексно, поэтому специалисты «СИБУР ПолиЛаб» приглашают заинтересованных слушателей на специальный вебинар, посвященный данной тематике и проводимый на платформе «Бизнес-практики «СИБУР», во время которого можно задать вопросы и получить индивидуальную консультацию.
Посмотреть в журнале