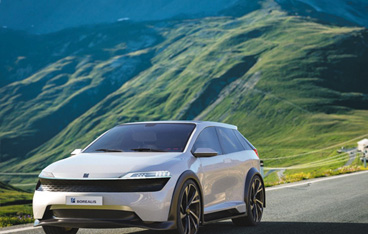
24.11.2023
Использование вторсырья: технологические новинки
То, что еще вчера казалось невозможным в секторе рециклинга, сегодня становится реальностью: полистирольные отходы превращаются в новые материалы, а тетрапак вполне можно разделить и вернуть в производство. Однако специалисты не останавливаются на достигнутом и все шире включают вторичное сырье в производство новой, коммерчески успешной продукции. Журнал «Пластикс» знакомит читателей с зарубежными инновациями в этой области.
Автопластики из вторсырья
Компании Borouge PLC и Borealis объявили о выпуске двух новых полимерных материалов для автомобильной промышленности, которые на 70% состоят из вторсырья. Это первые экологичные материалы, разработанные на заводе Borouge Compounding Manufacturing Plant (CMP), расположенном в Шанхае. «Запуск наших новейших продуктов свидетельствует о нашей приверженности принципам устойчивого развития. Используя переработанные материалы и разрабатывая продукты с меньшим углеродным следом, мы демонстрируем, что цели экономики замкнутого цикла вполне достижимы сегодня», — говорит Райнер Хефлинг, главный исполнительный директор Borouge.
По заверению производителей, новые ПП-марки, на 70% изготовленные из переработанных материалов, извлеченных из бытовых отходов (PCR), обеспечивают такие же характеристики и качество, что и исходные компаунды. Первый продукт GD3565SYC представляет собой армированный стекловолокном полипропилен, содержащий 50% PCR. Материал обеспечивает простоту обработки и долговременную термостойкость, благодаря этим характеристикам считается идеальным для выполнения защиты днища кузова, кронштейнов бампера и конструкционных деталей автомобилей. Второй материал марки ED0701SYC представляет собой полипропилен без наполнителя, предназначенный для изготовления колесных арок и других внешних компонентов, и содержит до 70% смеси полипропилена и полиэтилена, полученных из отходов.
Крышка из ПЭТ
Переработка бутылок из полиэтилентерефталата — один из самых успешных секторов рециклинга. После сбора на этапе сортировки бутылки должны быть отделены от крышек, обычно изготовленных из полипропилена или полиэтилена. В настоящий момент не все бутылки собираются вместе с крышками, однако все изменится в Европе после вступления в 2024 году в силу различных законодательных актов, требующих использования привязанных к пластиковой упаковке колпачков и крышек. Новый норматив увеличит спрос на разработку такой упаковки из мономатериала.
Американская компания Origin Materials увидела зарождение нового тренда и создала крышки для бутылок, полностью изготовленные из ПЭТ, что позволяет отправлять ПЭТ-упаковку после использования на переработку целиком.
«Производство бутылок, крышек и укупорочных средств, полностью изготовленных из ПЭТ, является очевидным шагом в сфере производства упаковки. С помощью созданной нами технологии мы можем производить колпачки из полностью вторичного ПЭТ или из ПЭТ, полученного на основе биологического сырья, причем их стоимость вполне конкурентоспособна», — говорит Джон Бисселл, соучредитель и генеральный директор Origin Materials.
Компания Origin Materials разработала технологическую платформу, использующую непищевое сырье растительного происхождения — целлюлозу, из которой в результате каталитических реакций выделяется хлорметилфурфурол, а он в свою очередь преобразуется в параксилол — один из компонентов, необходимых для производства полиэтилентерефталата.
С точки зрения свойств ПЭТ по сравнению с полиолефинами (ПЭВП и ПП) обеспечивает повышенную барьерную защиту от кислорода и СО2.
Поролон из 80% вторичного полиола
Еще в 2021 году компания Neveon (входит в Greiner Group) объединилась с концерном BASF для разработки проекта, позволяющего замкнуть цикл жизненного использования поролоновых матрасов. В результате был разработан метод химической переработки старых ПУ-матрасов, а полиол на основе ископаемого топлива заменен на высококачественный вторично переработанный реполиол. Это решение можно считать крупным технологическим прорывом.
Neveon превратил этот реполиол в поролон, содержащий 80% вторичного материала, и использовал его для производства большого количества полноценных матрасов. «Главная задача при производстве пеноблоков с таким высоким содержанием реполиола, полученного из старых матрасов, заключалась в оптимизации рецептуры и производственных процессов, ведь все качественные характеристики (высокая воздухопроницаемость и идеальная структура ячеек пены) должны быть идентичны свойствам матрасов, изготовленных из первичного полиола», — отмечает Роланд Кремер, вице-президент группы R&D Innovation Excellence в компании Neveon.
Помимо полиолов для производства пенополиуретана также необходимы изоцианаты. Поскольку они пока недоступны во вторично переработанном виде, а реполиолы еще далеки от того, чтобы стать широкодоступными в коммерческих целях, Neveon переоборудовал два своих завода в городе Кремсмюнстер в Австрии, чтобы приспособить площадку для получения максимально сбалансированного по массе (BMB) и экологичного сырья.
Чтобы матрасы были максимально удобными в эксплуатации, чаще всего их создают из различных типов пеноматериалов, которые скрепляются вместе, однако это затрудняет дальнейшую переработку изделий. Специалисты Neveon нашли решение и этой проблемы: пена из реполиола соединяется с одним из пенопластов, сертифицированных по стандарту REDcert (европейская система сертификации качества REDcert оценивает показатели устойчивости производства и управления, документацию по прослеживаемости и оценку выбросов парниковых газов) без клея за счет дизайна, напоминающего застежку-молнию. Отказ от применения клея означает, что соединенные полиуретановые блоки в матрасе не только не содержат посторонних материалов, но и легко разъединяются для максимально простой и эффективной вторичной переработки.
Разделение слоев многослойной пленки
Многослойные пленки используются для широкого спектра упаковочных материалов, особенно в пищевой промышленности. Европейское, а теперь и российское законодательство ужесточают требования в отношении как доли переработки полимерной упаковки, так и пригодности подобных изделий для рециклинга.
Однако переработка многослойной пленки, массово используемой для создания упаковки (в том числе термоформуемой), до сегодняшнего момента считалась одной из самых сложных задач, так как такие изделия изготавливаются из разных материалов, соединение которых обеспечивает нужный уровень прочности и барьерности.
Совместный проект компаний BASF, Krones, SUDPACK и Tomra продемонстрировал, что можно разделить многослойную упаковку из ПЭТ/ПЭ на отдельные компоненты и вернуть полимеры в производство в качестве сырья, при этом процесс переработки может быть реализован с использованием существующей инфраструктуры.
Во время первого промышленного испытания, проведенного на пилотном заводе Krones во Фленсбурге (Германия), партнеры смогли полностью разделить до 69% компонентов ПЭТ/ПЭ и частично разделить еще 12%.
Первый этап проекта стартовал в начале 2021 года, когда компания Tomra осуществила сортировку термоформованной упаковки из ПЭТ/ПЭ, изготовленную компанией SUDPACK с использованием «разделяющего клея», разработанного BASF. «Нашим вкладом в проект стал наш многолетний опыт в области ламинирования пленок и листов для пищевой, непищевой и медицинской упаковки. Мы предложили использовать ламинат на водной основе от компании BASF, который позволяет легко отделять слои путем горячей промывки щелочью», — говорит Каролин Гримбахер, управляющий партнер компании SUDPACK.
Чтобы замкнуть цикл материалов, вторично перерабатываемые многослойные пленки сначала должны быть отсортированы из потока отходов, и главное — отделены от изделий, не подлежащих рециклингу. «Система AUTOSORTTM, базирующаяся на технологии NIR (измерения в диапазоне ближнего ИК-спектра), способна обнаруживать многослойную упаковку из ПЭТ, содержащую клей BASF», — объясняет Давид Рюссманн, менеджер по специальным проектам компании Tomra.
В июле 2022 года к команде проекта присоединилась компания Krones, которая, помимо прочего, разрабатывает системы вторичной переработки пластиков в промышленных масштабах. Стандартный процесс горячей промывки, обычно используемый для переработки ПЭТ, был успешно применен, и в результате разделенные ПЭТ и ПЭ могут быть повторно использованы в качестве мономатериалов.
«На нашем предприятии мы подтвердили, что расслоение многослойных пленок работает. Тем не менее разделение пленок можно улучшить за счет оптимизации отдельных параметров процесса, а также, например, изменения размера хлопьев», — объясняет Тор Лакс, руководитель отдела технологических решений по переработке в фирме Krones.
«Наши клеи Epotal® на водной основе уже показали очень хорошие результаты при разделении многослойной упаковки в лаборатории. Мы считаем огромным успехом то, что нам удалось полностью разделить 69% упаковки во время нашего первого промышленного испытания. Мы уверены, что сможем еще больше увеличить этот показатель, оптимизировав рецептуру клея», — заявляет Кресимир Кьюл, специалист по коммерческому маркетингу промышленных клеев в BASF SE.
Посмотреть в журнале
Автопластики из вторсырья
Компании Borouge PLC и Borealis объявили о выпуске двух новых полимерных материалов для автомобильной промышленности, которые на 70% состоят из вторсырья. Это первые экологичные материалы, разработанные на заводе Borouge Compounding Manufacturing Plant (CMP), расположенном в Шанхае. «Запуск наших новейших продуктов свидетельствует о нашей приверженности принципам устойчивого развития. Используя переработанные материалы и разрабатывая продукты с меньшим углеродным следом, мы демонстрируем, что цели экономики замкнутого цикла вполне достижимы сегодня», — говорит Райнер Хефлинг, главный исполнительный директор Borouge.
По заверению производителей, новые ПП-марки, на 70% изготовленные из переработанных материалов, извлеченных из бытовых отходов (PCR), обеспечивают такие же характеристики и качество, что и исходные компаунды. Первый продукт GD3565SYC представляет собой армированный стекловолокном полипропилен, содержащий 50% PCR. Материал обеспечивает простоту обработки и долговременную термостойкость, благодаря этим характеристикам считается идеальным для выполнения защиты днища кузова, кронштейнов бампера и конструкционных деталей автомобилей. Второй материал марки ED0701SYC представляет собой полипропилен без наполнителя, предназначенный для изготовления колесных арок и других внешних компонентов, и содержит до 70% смеси полипропилена и полиэтилена, полученных из отходов.
Крышка из ПЭТ
Переработка бутылок из полиэтилентерефталата — один из самых успешных секторов рециклинга. После сбора на этапе сортировки бутылки должны быть отделены от крышек, обычно изготовленных из полипропилена или полиэтилена. В настоящий момент не все бутылки собираются вместе с крышками, однако все изменится в Европе после вступления в 2024 году в силу различных законодательных актов, требующих использования привязанных к пластиковой упаковке колпачков и крышек. Новый норматив увеличит спрос на разработку такой упаковки из мономатериала.
Американская компания Origin Materials увидела зарождение нового тренда и создала крышки для бутылок, полностью изготовленные из ПЭТ, что позволяет отправлять ПЭТ-упаковку после использования на переработку целиком.
«Производство бутылок, крышек и укупорочных средств, полностью изготовленных из ПЭТ, является очевидным шагом в сфере производства упаковки. С помощью созданной нами технологии мы можем производить колпачки из полностью вторичного ПЭТ или из ПЭТ, полученного на основе биологического сырья, причем их стоимость вполне конкурентоспособна», — говорит Джон Бисселл, соучредитель и генеральный директор Origin Materials.
Компания Origin Materials разработала технологическую платформу, использующую непищевое сырье растительного происхождения — целлюлозу, из которой в результате каталитических реакций выделяется хлорметилфурфурол, а он в свою очередь преобразуется в параксилол — один из компонентов, необходимых для производства полиэтилентерефталата.
С точки зрения свойств ПЭТ по сравнению с полиолефинами (ПЭВП и ПП) обеспечивает повышенную барьерную защиту от кислорода и СО2.
Поролон из 80% вторичного полиола
Еще в 2021 году компания Neveon (входит в Greiner Group) объединилась с концерном BASF для разработки проекта, позволяющего замкнуть цикл жизненного использования поролоновых матрасов. В результате был разработан метод химической переработки старых ПУ-матрасов, а полиол на основе ископаемого топлива заменен на высококачественный вторично переработанный реполиол. Это решение можно считать крупным технологическим прорывом.
Neveon превратил этот реполиол в поролон, содержащий 80% вторичного материала, и использовал его для производства большого количества полноценных матрасов. «Главная задача при производстве пеноблоков с таким высоким содержанием реполиола, полученного из старых матрасов, заключалась в оптимизации рецептуры и производственных процессов, ведь все качественные характеристики (высокая воздухопроницаемость и идеальная структура ячеек пены) должны быть идентичны свойствам матрасов, изготовленных из первичного полиола», — отмечает Роланд Кремер, вице-президент группы R&D Innovation Excellence в компании Neveon.
Помимо полиолов для производства пенополиуретана также необходимы изоцианаты. Поскольку они пока недоступны во вторично переработанном виде, а реполиолы еще далеки от того, чтобы стать широкодоступными в коммерческих целях, Neveon переоборудовал два своих завода в городе Кремсмюнстер в Австрии, чтобы приспособить площадку для получения максимально сбалансированного по массе (BMB) и экологичного сырья.
Чтобы матрасы были максимально удобными в эксплуатации, чаще всего их создают из различных типов пеноматериалов, которые скрепляются вместе, однако это затрудняет дальнейшую переработку изделий. Специалисты Neveon нашли решение и этой проблемы: пена из реполиола соединяется с одним из пенопластов, сертифицированных по стандарту REDcert (европейская система сертификации качества REDcert оценивает показатели устойчивости производства и управления, документацию по прослеживаемости и оценку выбросов парниковых газов) без клея за счет дизайна, напоминающего застежку-молнию. Отказ от применения клея означает, что соединенные полиуретановые блоки в матрасе не только не содержат посторонних материалов, но и легко разъединяются для максимально простой и эффективной вторичной переработки.
Разделение слоев многослойной пленки
Многослойные пленки используются для широкого спектра упаковочных материалов, особенно в пищевой промышленности. Европейское, а теперь и российское законодательство ужесточают требования в отношении как доли переработки полимерной упаковки, так и пригодности подобных изделий для рециклинга.
Однако переработка многослойной пленки, массово используемой для создания упаковки (в том числе термоформуемой), до сегодняшнего момента считалась одной из самых сложных задач, так как такие изделия изготавливаются из разных материалов, соединение которых обеспечивает нужный уровень прочности и барьерности.
Совместный проект компаний BASF, Krones, SUDPACK и Tomra продемонстрировал, что можно разделить многослойную упаковку из ПЭТ/ПЭ на отдельные компоненты и вернуть полимеры в производство в качестве сырья, при этом процесс переработки может быть реализован с использованием существующей инфраструктуры.
Во время первого промышленного испытания, проведенного на пилотном заводе Krones во Фленсбурге (Германия), партнеры смогли полностью разделить до 69% компонентов ПЭТ/ПЭ и частично разделить еще 12%.
Первый этап проекта стартовал в начале 2021 года, когда компания Tomra осуществила сортировку термоформованной упаковки из ПЭТ/ПЭ, изготовленную компанией SUDPACK с использованием «разделяющего клея», разработанного BASF. «Нашим вкладом в проект стал наш многолетний опыт в области ламинирования пленок и листов для пищевой, непищевой и медицинской упаковки. Мы предложили использовать ламинат на водной основе от компании BASF, который позволяет легко отделять слои путем горячей промывки щелочью», — говорит Каролин Гримбахер, управляющий партнер компании SUDPACK.
Чтобы замкнуть цикл материалов, вторично перерабатываемые многослойные пленки сначала должны быть отсортированы из потока отходов, и главное — отделены от изделий, не подлежащих рециклингу. «Система AUTOSORTTM, базирующаяся на технологии NIR (измерения в диапазоне ближнего ИК-спектра), способна обнаруживать многослойную упаковку из ПЭТ, содержащую клей BASF», — объясняет Давид Рюссманн, менеджер по специальным проектам компании Tomra.
В июле 2022 года к команде проекта присоединилась компания Krones, которая, помимо прочего, разрабатывает системы вторичной переработки пластиков в промышленных масштабах. Стандартный процесс горячей промывки, обычно используемый для переработки ПЭТ, был успешно применен, и в результате разделенные ПЭТ и ПЭ могут быть повторно использованы в качестве мономатериалов.
«На нашем предприятии мы подтвердили, что расслоение многослойных пленок работает. Тем не менее разделение пленок можно улучшить за счет оптимизации отдельных параметров процесса, а также, например, изменения размера хлопьев», — объясняет Тор Лакс, руководитель отдела технологических решений по переработке в фирме Krones.
«Наши клеи Epotal® на водной основе уже показали очень хорошие результаты при разделении многослойной упаковки в лаборатории. Мы считаем огромным успехом то, что нам удалось полностью разделить 69% упаковки во время нашего первого промышленного испытания. Мы уверены, что сможем еще больше увеличить этот показатель, оптимизировав рецептуру клея», — заявляет Кресимир Кьюл, специалист по коммерческому маркетингу промышленных клеев в BASF SE.
Посмотреть в журнале