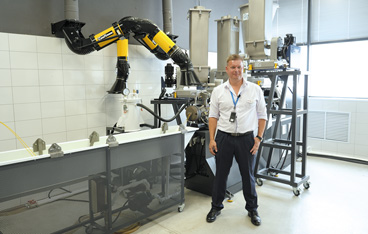
14.11.2024
Компания «Манро» представила двухшнековый экструдер
4 сентября в рамках Дня открытых дверей, прошедшего в городе Тольятти, компания «Манро» осуществила успешный запуск экструзионной линии, оснащенной двухшнековым экструдером DSE27 с сонаправленно вращающимися шнеками. Данное оборудование не имеет аналогов в стране; линия полностью спроектирована, сконструирована и изготовлена специалистами «Манро», в том числе такие компоненты, как периферийное оборудование и программное обеспечение, управляющее всем комплексом. Представители журнала «Пластикс» и заказчики компании — производители и переработчики пластмасс — посетили данное мероприятие и познакомились с производственной «кухней» завода.
На Дне открытых дверей присутствовали более 40 представителей компаний из секторов компаундирования, производства пластмассовых изделий и лакокрасочной продукции. Гости ознакомились с технологическими мощностями компании «Манро» и процессом производства запасных частей и комплектующих к экструдерам.
Экскурсия по предприятию
Собравшимся показали как уже работающие цеха, так и строящиеся. Экскурсия началась с зоны приемки-отгрузки ремонтируемых деталей и склада заготовок. Гости мероприятия отметили, что все хранящиеся на стеллажах материалы и изделия подписаны: сквозная маркировка помогает проследить жизненный цикл запчасти до конца срока ее эксплуатации. Три года назад на заводе была внедрена система управления, ведущая учет уникальных ID-номеров каждой детали.
Закупленные заготовки в виде металлических прутков проходят обязательный входной контроль в специализированной лаборатории. Если же требуется более глубокий анализ материала, компания привлекает Тольяттинский государственный университет. В «Манро» изначально предъявляют высокие требования к качеству сталей, чтобы не подводить ни себя, ни заказчиков.
На распиловочном участке используется современная немецкая пила, причем процесс автоматизирован: компания стремится оптимизировать все процессы и использует станки с ЧПУ, высвобождая таким образом рабочую силу для более тонких процессов.
Цех мехобработки включает участок крупносерийной (здесь из заготовок вытачиваются шнековые элементы и осуществляется профилирование; обработка идет сразу чистовая с нужными допусками, что позволяет избежать погрешностей) и фрезерной обработки (готовятся сопутствующие детали — баррели, фильеры, гильзы).
В цехах установлено дорогостоящее оборудование: японские и немецкие токарно-фрезерные станки, оснащенные роботами-манипуляторами, фрезерные немецкие и китайские центры. Для оптимизации энергозатрат на каждом станке установлен дисплей, на который выводится показатель эффективности работы машины: нормальное соотношение режимов «наладка/обработка» составляет 20/80. При понижении параметров технологи проводят анализ загрузки оборудования и линейного персонала, а далее оптимизацию для повышения этого показателя, так как он является одним из приоритетных.
Инженер-технолог подбирает загрузку каждого станка, таким образом наладчик получает готовую программу работы.
Гостям показали также участок ОТК, где осуществляется межоперационный (например, для деталей, поступивших после термообработки, которую выполняет сторонняя организация) и итоговый контроль. Проверяется все: геометрические размеры, твердость, шероховатость и другие необходимые параметры. Весь инструмент для тестирования откалиброван и поверен в сертифицированном центре.
На участке электроэрозии обрабатываются шлицевые поверхности. Каждый станок здесь снабжен устройством цифровой индикации, отслеживающим качество выполнения операций. Автоматизация процессов настроена таким образом, что 12 станков в смену обслуживает всего лишь один оператор.
В новом помещении, где в настоящее время проходит ремонт, уже укомплектован и запущен в эксплуатацию участок с новым шлифовальным оборудованием.
Завершается цикл изготовления любой детали операциями итогового контроля, маркировки, упаковки и отправки заказчику.
Экскурсанты отметили не только чистоту в цехах, стильный дизайн офисных помещений и шоурума, но и наличие такого непривычного для завода элемента, как барная зона, которая предназначена для проведения корпоративов и праздников.
Презентация экструдера DSE27
Главным событием мероприятия, конечно, стала презентация экструзионной линии на базеэкструдера DSE27 с сонаправленно вращающимися шнеками. Все элементы линии, кроме весовых дозаторов Transcell, выполнены специалистами фирмы «Манро». Представленная линия способна производить до 130 кг гранулированной продукции в час. Диапазон применения включает широкий спектр материалов от полимеров до пищевых продуктов, порошковых красок и фармпрепаратов. Предприятие готово предоставить индивидуальную конфигурацию линии в зависимости от потребностей заказчика.
Во время презентации отмечались следующие особенности комплектации экструдера DSE27:
— электрический синхронный двигатель с водяным охлаждением и частотный преобразователь с векторным управлением обеспечивает непревзойденную эффективность и надежность;
— принцип «единой панели» управления, позволяющий централизованно управлять всеми системами экструдера и периферийного оборудования с одного рабочего места, делает процесс управления простым и интуитивным;
— трехуровневая система вибродиагностики контроля состояния редуктора гарантирует длительный срок эксплуатации даже в самых сложных условиях;
— высокомоментное исполнение механической части и усиленная конструкция станины обеспечивают стабильность и долговечность при любых нагрузках;
— система вакуумной дегазации, разработанная «Манро», с уникальной системой завихрения и быстрой очистки, гарантирует высокоэффективное удаление газов из материала;
— технологическая часть с повышенным свободным объемом 1.65 увеличивает производительность до 30% и обеспечивает гибкость переработки различных рецептур;
— система многоуровневой защиты, аналогичная решениям ведущих европейских производителей, гарантирует высокий уровень безопасности и надежности оборудования.
«Хочу и могу!»
После презентации Дмитрий Мандычев, основатель и директор компании «Манро», дал небольшое интервью журналу «Пластикс».
— Дмитрий, как бы вы могли охарактеризовать сегодняшнюю ситуацию на российском рынке экструзионного оборудования?
— Никто в России не производит экструдеры, эту технику везут из Китая. Оборудование везут долго, оно может зависнуть на таможне, и, конечно, есть проблемы с платежами. Но купить экструдер — еще полбеды, помимо этого нужны пусконаладка и сервисное обслуживание. Получить это у китайского производителя очень сложно, максимум — вам предоставят возможность связи по Интернету. Мы надеемся, отечественные экструдеры «Манро» смогут решить эту проблему.
— Как вы пришли к идее сконструировать экструдер?
— Когда ушли немецкие производители с их оборудованием премиум-сегмента, образовалось окно возможностей. Если мы сейчас попробуем заменить их продукцию машинами с теми же характеристиками, но по цене на 30% меньше (ведь основные узлы изготавливаются в России, и сборка тоже российская), то отечественные переработчики оценят это шаг. Мы решили выйти на рынок с экструдером, построенным по европейским стандартам в плане безопасности для оператора, производительности, надежности и долговечности при минимальных эксплуатационных затратах. У нас был успешный опыт поставок экструзионных запчастей на рынки Европы, так что мы понимаем, как удовлетворить запросы заказчика.
— Говорят, сегодня «Манро» занимает на рынке экструзионных запчастей положение монополиста. Это хорошо для вас или нет?
— Конкуренция на рынке есть — это китайские детали. Но я согласен, из российских производителей в данном сегменте мы действуем практически монопольно. Однако я рассматриваю это как большую ответственность. Мы не можем позволить себе срыв поставок, например. Сейчас, в условиях санкций, приходится активно развиваться и расширять мощности, чтобы закрыть потребности рынка, но ресурсы не всегда получается разворачивать быстро, а заказчик меж тем не готов думать о существующей в силу объективных причин инерциальности проектов. Первое место довольно жестко ограничивает нас…
— Дмитрий, зачем вам понадобился экструдер, если дела в компании и так идут хорошо?
— Вы видели сегодня на заводе, что прибыль инвестируется в расширение и улучшение качества производства, а не в яхты или дорогие машины. Мне интереснее справляться с вызовами жизни, в том числе, например, создать первый российский экструдер с сонаправленно вращающимися шнеками. Даже если мы не продадим ни одного, я все равно буду знать: я сделал это. Думаю, я живу по принципу «Хочу и могу!»
— Сегодня состоялся пробный запуск, но экструдеру еще предстоит обкатка?
— Безусловно, нужно время, чтобы обнаружить детские болезни, нюансы, требующие доработки. Мы это делаем вместе с нашими давними заказчиками, которые дают обратную связь. И я благодарен тем партнерам, которые на протяжении двух лет подготовки промышленной версии экструдера помогали нам.
— Что позволяет вам, Дмитрий, энергично развивать свой бизнес даже в непростых экономических условиях?
— Представьте, что вы бежите перед паровозом. Если остановитесь, то вы не выживете. Вот так должен себя чувствовать бизнес, который хочет жить. Ждать, когда откроются границы, бессмысленно — действовать нужно прямо сейчас: не расслабляясь, не почивая на лаврах. Дыхание «паровоза» я чувствую с 2009 года, и, честно говоря, уже просто не обращаю на это внимания — просто бегу. Плюс как перфекционист я люблю все новое и чистое. Чистота в цехах, современное оборудование, хорошие инструменты, приличные зарплаты — я стараюсь создать максимум условий для того, чтобы все сотрудники работали эффективно. Так что мы бежим вместе.
Подготовила Анна Виленс
Посмотреть в журнале
На Дне открытых дверей присутствовали более 40 представителей компаний из секторов компаундирования, производства пластмассовых изделий и лакокрасочной продукции. Гости ознакомились с технологическими мощностями компании «Манро» и процессом производства запасных частей и комплектующих к экструдерам.
Экскурсия по предприятию
Собравшимся показали как уже работающие цеха, так и строящиеся. Экскурсия началась с зоны приемки-отгрузки ремонтируемых деталей и склада заготовок. Гости мероприятия отметили, что все хранящиеся на стеллажах материалы и изделия подписаны: сквозная маркировка помогает проследить жизненный цикл запчасти до конца срока ее эксплуатации. Три года назад на заводе была внедрена система управления, ведущая учет уникальных ID-номеров каждой детали.
Закупленные заготовки в виде металлических прутков проходят обязательный входной контроль в специализированной лаборатории. Если же требуется более глубокий анализ материала, компания привлекает Тольяттинский государственный университет. В «Манро» изначально предъявляют высокие требования к качеству сталей, чтобы не подводить ни себя, ни заказчиков.
На распиловочном участке используется современная немецкая пила, причем процесс автоматизирован: компания стремится оптимизировать все процессы и использует станки с ЧПУ, высвобождая таким образом рабочую силу для более тонких процессов.
Цех мехобработки включает участок крупносерийной (здесь из заготовок вытачиваются шнековые элементы и осуществляется профилирование; обработка идет сразу чистовая с нужными допусками, что позволяет избежать погрешностей) и фрезерной обработки (готовятся сопутствующие детали — баррели, фильеры, гильзы).
В цехах установлено дорогостоящее оборудование: японские и немецкие токарно-фрезерные станки, оснащенные роботами-манипуляторами, фрезерные немецкие и китайские центры. Для оптимизации энергозатрат на каждом станке установлен дисплей, на который выводится показатель эффективности работы машины: нормальное соотношение режимов «наладка/обработка» составляет 20/80. При понижении параметров технологи проводят анализ загрузки оборудования и линейного персонала, а далее оптимизацию для повышения этого показателя, так как он является одним из приоритетных.
Инженер-технолог подбирает загрузку каждого станка, таким образом наладчик получает готовую программу работы.
Гостям показали также участок ОТК, где осуществляется межоперационный (например, для деталей, поступивших после термообработки, которую выполняет сторонняя организация) и итоговый контроль. Проверяется все: геометрические размеры, твердость, шероховатость и другие необходимые параметры. Весь инструмент для тестирования откалиброван и поверен в сертифицированном центре.
На участке электроэрозии обрабатываются шлицевые поверхности. Каждый станок здесь снабжен устройством цифровой индикации, отслеживающим качество выполнения операций. Автоматизация процессов настроена таким образом, что 12 станков в смену обслуживает всего лишь один оператор.
В новом помещении, где в настоящее время проходит ремонт, уже укомплектован и запущен в эксплуатацию участок с новым шлифовальным оборудованием.
Завершается цикл изготовления любой детали операциями итогового контроля, маркировки, упаковки и отправки заказчику.
Экскурсанты отметили не только чистоту в цехах, стильный дизайн офисных помещений и шоурума, но и наличие такого непривычного для завода элемента, как барная зона, которая предназначена для проведения корпоративов и праздников.
Презентация экструдера DSE27
Главным событием мероприятия, конечно, стала презентация экструзионной линии на базеэкструдера DSE27 с сонаправленно вращающимися шнеками. Все элементы линии, кроме весовых дозаторов Transcell, выполнены специалистами фирмы «Манро». Представленная линия способна производить до 130 кг гранулированной продукции в час. Диапазон применения включает широкий спектр материалов от полимеров до пищевых продуктов, порошковых красок и фармпрепаратов. Предприятие готово предоставить индивидуальную конфигурацию линии в зависимости от потребностей заказчика.
Во время презентации отмечались следующие особенности комплектации экструдера DSE27:
— электрический синхронный двигатель с водяным охлаждением и частотный преобразователь с векторным управлением обеспечивает непревзойденную эффективность и надежность;
— принцип «единой панели» управления, позволяющий централизованно управлять всеми системами экструдера и периферийного оборудования с одного рабочего места, делает процесс управления простым и интуитивным;
— трехуровневая система вибродиагностики контроля состояния редуктора гарантирует длительный срок эксплуатации даже в самых сложных условиях;
— высокомоментное исполнение механической части и усиленная конструкция станины обеспечивают стабильность и долговечность при любых нагрузках;
— система вакуумной дегазации, разработанная «Манро», с уникальной системой завихрения и быстрой очистки, гарантирует высокоэффективное удаление газов из материала;
— технологическая часть с повышенным свободным объемом 1.65 увеличивает производительность до 30% и обеспечивает гибкость переработки различных рецептур;
— система многоуровневой защиты, аналогичная решениям ведущих европейских производителей, гарантирует высокий уровень безопасности и надежности оборудования.
«Хочу и могу!»
После презентации Дмитрий Мандычев, основатель и директор компании «Манро», дал небольшое интервью журналу «Пластикс».
— Дмитрий, как бы вы могли охарактеризовать сегодняшнюю ситуацию на российском рынке экструзионного оборудования?
— Никто в России не производит экструдеры, эту технику везут из Китая. Оборудование везут долго, оно может зависнуть на таможне, и, конечно, есть проблемы с платежами. Но купить экструдер — еще полбеды, помимо этого нужны пусконаладка и сервисное обслуживание. Получить это у китайского производителя очень сложно, максимум — вам предоставят возможность связи по Интернету. Мы надеемся, отечественные экструдеры «Манро» смогут решить эту проблему.
— Как вы пришли к идее сконструировать экструдер?
— Когда ушли немецкие производители с их оборудованием премиум-сегмента, образовалось окно возможностей. Если мы сейчас попробуем заменить их продукцию машинами с теми же характеристиками, но по цене на 30% меньше (ведь основные узлы изготавливаются в России, и сборка тоже российская), то отечественные переработчики оценят это шаг. Мы решили выйти на рынок с экструдером, построенным по европейским стандартам в плане безопасности для оператора, производительности, надежности и долговечности при минимальных эксплуатационных затратах. У нас был успешный опыт поставок экструзионных запчастей на рынки Европы, так что мы понимаем, как удовлетворить запросы заказчика.
— Говорят, сегодня «Манро» занимает на рынке экструзионных запчастей положение монополиста. Это хорошо для вас или нет?
— Конкуренция на рынке есть — это китайские детали. Но я согласен, из российских производителей в данном сегменте мы действуем практически монопольно. Однако я рассматриваю это как большую ответственность. Мы не можем позволить себе срыв поставок, например. Сейчас, в условиях санкций, приходится активно развиваться и расширять мощности, чтобы закрыть потребности рынка, но ресурсы не всегда получается разворачивать быстро, а заказчик меж тем не готов думать о существующей в силу объективных причин инерциальности проектов. Первое место довольно жестко ограничивает нас…
— Дмитрий, зачем вам понадобился экструдер, если дела в компании и так идут хорошо?
— Вы видели сегодня на заводе, что прибыль инвестируется в расширение и улучшение качества производства, а не в яхты или дорогие машины. Мне интереснее справляться с вызовами жизни, в том числе, например, создать первый российский экструдер с сонаправленно вращающимися шнеками. Даже если мы не продадим ни одного, я все равно буду знать: я сделал это. Думаю, я живу по принципу «Хочу и могу!»
— Сегодня состоялся пробный запуск, но экструдеру еще предстоит обкатка?
— Безусловно, нужно время, чтобы обнаружить детские болезни, нюансы, требующие доработки. Мы это делаем вместе с нашими давними заказчиками, которые дают обратную связь. И я благодарен тем партнерам, которые на протяжении двух лет подготовки промышленной версии экструдера помогали нам.
— Что позволяет вам, Дмитрий, энергично развивать свой бизнес даже в непростых экономических условиях?
— Представьте, что вы бежите перед паровозом. Если остановитесь, то вы не выживете. Вот так должен себя чувствовать бизнес, который хочет жить. Ждать, когда откроются границы, бессмысленно — действовать нужно прямо сейчас: не расслабляясь, не почивая на лаврах. Дыхание «паровоза» я чувствую с 2009 года, и, честно говоря, уже просто не обращаю на это внимания — просто бегу. Плюс как перфекционист я люблю все новое и чистое. Чистота в цехах, современное оборудование, хорошие инструменты, приличные зарплаты — я стараюсь создать максимум условий для того, чтобы все сотрудники работали эффективно. Так что мы бежим вместе.
Подготовила Анна Виленс
Посмотреть в журнале