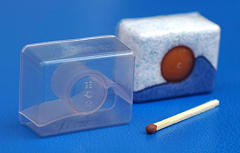
Литье ПВС: новая завоеванная территория
Уникальные свойства ПВС
Поливиниловый спирт (ПВС) впервые был получен в 1924 году немецкими химиками Вильгельмом Германном и Вольфрамом Хэнелем и, таким образом, является одним из старейших полимеров. В связи с этим интересно отметить, что ПВС нельзя получить непосредственно из мономера винилового спирта, а можно лишь путем гидролитической реакции («омыления») с гидроксидом натрия из еще более старого пластмассового материала — поливинилацетата (ПВА), впервые синтезированного также немцем, химиком Фрицем Клатте еще в 1913 году.
Этот процесс позволяет удалять ацетатные группы, превращая их в гидроксильные, благодаря чему вещество приобретает свои характерные свойства. Химическая формула ПВС — (C2H4O)n, где n обозначает количество повторяющихся мономерных звеньев.
Виды поливинилового спирта
Производство поливинилового спирта можно контролировать с помощью полного или частичного преобразования ПВА в ПВС. Чем больше остаточного ацетата содержит поливиниловый спирт, тем ниже его растворимость в воде. Различное содержание ацетата также вызывает изменение температуры плавления, вязкости расплава и технологических параметров ПВС. В то время как температура плавления полностью гидролизованного ПВС составляет около 230°C, для частично гидролизованного спирта она лежит в диапазоне от 180 до 200°C. Плотность поливинилового спирта (ПВС) варьируется в зависимости от степени гидролиза и молекулярной массы. Обычно она находится в диапазоне от 1,19 до 1,31 г/см³.
Оба этих пластика объединяет меньшая длина полимерных цепей в сравнении с другими пластмассовыми материалами. От одной партии к другой она колеблется от 100 до 5000 в зависимости от условий технологического процесса. Конечные механические свойства ПВС также зависят от содержания в нем воды, поскольку диффундирующая вода действует как смягчающий агент. В этой связи при высокой влажности воздуха ПВС теряет часть своей прочности на разрыв, но выигрывает в эластичности.
- Низкомолекулярный материал обладает низкой вязкостью и используется в косметике и красках, среднемолекулярный подходит для клеев и пленок, а высокомолекулярный — для барьерных покрытий и упаковки
- ПВС выпускается в виде порошка, гранул или готовых растворов, применяемых в косметике и медицине. Добавки, такие как пластификаторы или модификаторы, повышают его эластичность, термостойкость и адгезию, расширяя применение в промышленных покрытиях и текстильной обработке.
- Существуют специализированные виды, включая водорастворимые пленки, косметические составы и медицинские формы. Благодаря разнообразию характеристик ПВС востребован в текстильной, упаковочной, косметической и фармацевтической промышленности.
Применение поливинилового спирта
Кроме того, ПВС легко образует пленку и обладает хорошей смачивающей способностью. Поливиниловый спирт используется в следующих отраслях:
Опасности использования
ПВС считается безопасным материалом, но при работе с концентрированными растворами следует соблюдать меры предосторожности, так как возможны раздражения кожи и глаз. Утилизация отходов должна осуществляться в соответствии с экологическими нормами.
Новая сфера — литье ПВС
На протяжении своей почти столетней истории расплавы поливинилового спирта практически никогда не перерабатывались литьем под давлением. Основными причинами этого были как отсутствие идей для продукции, так и колебания ключевых параметров материала до ±20%.
Поворотным стал 2003 год, когда одна химическая компания мирового уровня отправила запрос в австрийскую фирму Buzek Kunststoffverarbeitung на оснащение завода оборудованием для литья под давлением многокамерных контейнеров для гранулированного чистящего средства для посудомоечных машин. Андреас Хубер, управляющий и генеральный директор Buzek Holding GmbH (Австрия) и Buzek Plastic Poland (Польша), вспоминает: «Новые сложные технические задачи, связанные с процессами литьевого формования, всегда пленяли меня. Фундамент по данному направлению был заложен, еще когда я работал инженером в компании Battenfeld и занимался развитием технологий переработки специальных материалов. Я с трудом мог поверить, что никто до меня не изготавливал серийно детали из поливинилового спирта. Поверил я в это лишь после первых испытаний на пластификацию, результаты которых были донельзя похожи на поведение обойного клея: материал плотно прилипал к пресс-форме. Неудивительно, что поливиниловый спирт присутствует в составе любого клея для бумаги. Теперь я знал, что до серийного производства предстоит пройти длинный путь. Но при этом я понимал, что в случае удачи у нашей продук- ции был бы огромный потенциал. Поэтому сегодня я очень рад, что мы с моим бизнес- партнером Гюнтером Бузеком смогли полу- чить в этом проекте поддержку руководства Wittmann Battenfeld. Вместе мы были в состоянии начать систематическую разработку соответствующей прикладной технологии».
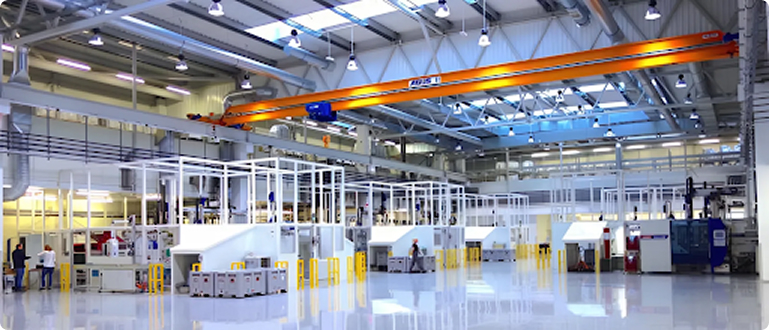
Завод Buzek Plastic Poland в польском городе Плонске, построенный согласно концепции Industry 4.0
После нескольких предварительных испытаний основой для литьевого материала стал ПВС низкой вязкости, изначально разработанный для бумажной промышленности. В ходе многочисленных испытаний с использованием различных вспомогательных добавок из него наконец-то был получен компаунд, который можно было перерабатывать методом литья под давлением. Тогда удалось изготовить первый тонкостенный контейнер размером 30´40´15 мм, сначала в 1-местной, затем в 4- и, наконец, в 12-местной пресс-форме. Испытания в технической лаборатории Wittmann Battenfeld на полностью электрических литьевых машинах BA 1000/500 CDK-SE и EM 1600/350 показали, что быстрый впрыск и высокоточный контроль давления впрыска ведут к положительным результатам. При этом пока что пришлось мириться с уровнем брака 15-20% по причине колебаний свойств материала от партии к партии.
От прикладной технологии — к реальному производству
На трех гидравлических машинах Wittmann Battenfeld HM 270/1330, оснащенных аккумуляторами для высокоскоростного впрыска, был выполнен переход от тестовой 12-местной к 32-местной горячека- нальной пресс-форме и начато серийное производство. Несмотря на многочисленные случаи аномальных значений параметров материала и связанного с этим высокого уровня брака, выпуск изделий не прекращался. Применялся ситуативный метод производства, состоящий в ручной настройке параметров на основе непрерывного наблюдения за поведением материала со 100-процентной визуальной проверкой готовых изделий обслуживающим персоналом на каждой машине.
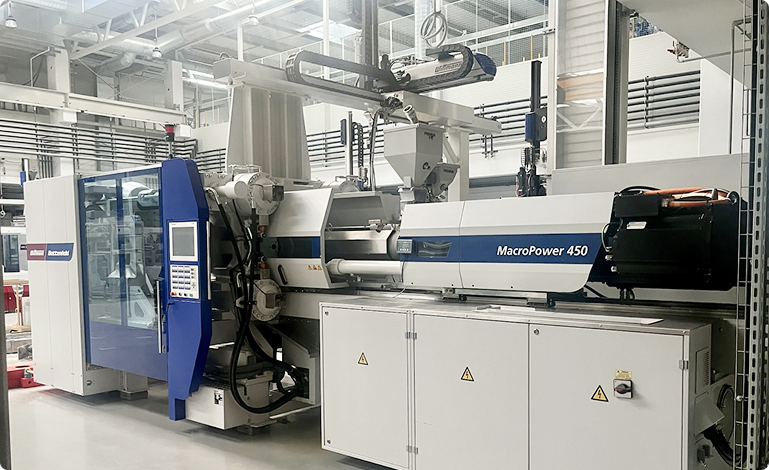
Производственные ячейки на базе машины Wittmann Battenfeld MacroPower E 450/2100
Примерно через год технология производства и состав материала были стабилизированы настолько, что стал возможным дальнейший рост мощностей. Поскольку дизайн продукции пока не менялся, продолжительность цикла оставалась неизменной — порядка 28 с при доле брака около 15%. Дополнительного улучшения требовал метод визуального осмотра изделий. Вместо контроля продукции в отдельности на каждом ТПА была внедрена централизованная система сбора и перемещения изделий от каждого ТПА к центральной станции осмотра, где все до единой детали подвергались визуальному контролю, выполняемому, как и прежде, рабочим персоналом завода.
Однако компания стремилась не только увеличить число гнезд, но и совместить это с сокращением времени цикла. В этих целях в тесном сотрудничестве с инженерами заказчика конструкция отли- ваемого изделия была переработана. Толщина стенок была выборочно уменьшена, что приве- ло к снижению массы изделия и сокращению времени цикла на 15%. Однако для этого требовались быстрые и мощные литьевые машины. По причине положительного прошлого опыта сотрудничества поставщиком вновь была выбрана компания Wittmann Battenfeld. Выбор пал на гидравлические машины HM 400/2250 с аккумуляторами для высокоскоростного впрыска, оснащенными роботами Wittmann и автоматизированными системами перемещения изделий по конвейерам.
Этот рост побудил компанию создать новую концепцию контроля качества готовых изделий, который стало невозможным выполнять с использованием человеческих ресурсов как с экономической точки зрения, так и по причине недостаточности ресурсов при такой высокой производительности. Для решения этой проблемы компания Buzek внедрила систему машин- ного визуального контроля с автоматической отбраковкой, которая все же не могла полностью заменить осмотр продукции персона- лом, поскольку была способна распознавать лишь общую законченность изделий, но не каждый из дефектов детально.
Новый завод согласно Industry 4.0
В 2012 году, когда производство насчитывало уже 19 ячеек, места для установки новых машин больше не было. Тогда для дальнейшего роста руководство Buzek Plastic приняло решение построить новый комплекс вне территории завода заказчика. Строительство помогло бы внедрить новейшие методы переработки, которые были невозможны на базе инфраструктуры и средств, существующих на старом предприятии. Была поставлена новая задача — полное сетевое объединение данных на всех этапах производства с дополнитель- ным средством автоматического контроля в рамках заранее установленных допусков по качеству согласно концепции Industry 4.0. Основная идея заключалась в создании автоматической системы с нулевым процентом брака путем автоматического взаимодействия всех процессов.
Параллельно с проектированием нового завода в тесном сотрудничестве с конечным заказчиком был начат процесс оптимизации и самого изделия с целью снизить себестои- мость продукции за счет дальнейшего сокращения ее массы и продолжительности вре- мени цикла. В результате масса изделия была снижена на 10% (при неизменных размерах изделий), а время цикла сокращено на 25%. Однако при этом мощность гидравлических машин была использована до предела, поэтому единственной разумной альтернативой стал переход на сервогидравлические машины для литья под давлением. В это время серво электрической машины требуемой мощности еще не было, и требовалась дополнительная работа по разработке оборудования. Последовал оживленный диалог Андреаса Хубера с инженерами Wittmann Battenfeld на предмет проработки требуемых технических характеристик. Наконец, была спроектирована абсолютно новая гибридная машина MacroPower E 450/2100 с гидравли- ческим двухпалатным узлом смыкания, развивающим усилие 450 т, и серво электрическим узлом впрыска размера 2100.
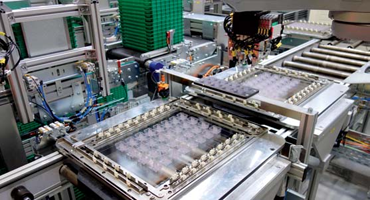
Перекладочные устройства отбраковывают все некондиционные изделия и заменяют их качественными
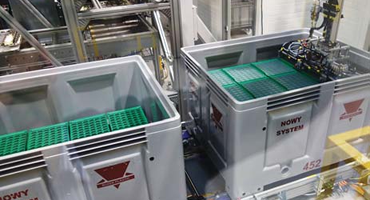
После проверки качества и отбраковки готовые изделия помещаются в лотки, а лотки — в коробки для отправки на фасовочно-упаковочную станцию
Каждая литьевая машина была преобразована в технологическую ячейку путем добавления линейного робота и автоматиза- ции для фотографирования готовых изделий с интегрированными станциями контроля, отбраковки и укладки изделий. Особое зна- чение для оценки качества продукции имеет система машинного зрения, адаптированная к значительно возросшим объемам производства и требованиям к качеству. Новая система, состоящая из 12 камер и комплекта зеркал, работает синхронно с циклом изготовления продукции, фотографируя каждое из 64 готовых изделий с пяти разных ракурсов и передавая снимки в систему анализа.
ПО этой системы способно распознавать дефекты 23 различных типов. Сразу же после прохождения через радиостанцию бракованные изделия отделяются прокладочным устройством и заменяются качественными из буфера. Это гарантирует, что на автоматическую упаковочную станцию поступают 100-процентно качественные детали. Все станции, входящие в периферийную систему транспортировки продукции, взаимодействуют друг с другом по специально разработанному логистическому алгоритму, который позволяет компенсировать возможные колебания техпроцессов.
В целом достигнутый на новом заводе уровень производительности представляет собой повод для гордости. За восемь лет не только более чем на 400% увеличился выпуска изделий в расчете на литейную ячейку, но и снизился процент брака с 15 до менее чем 3%. Сегодня все полностью автоматические ячейки на новом заводе снова используются на 100%. Следующий шаг развития будет заключаться в замене старого оборудования на новое. Опять же, это связано не только с увеличением объемов продукции, но и с повышением эффективности.