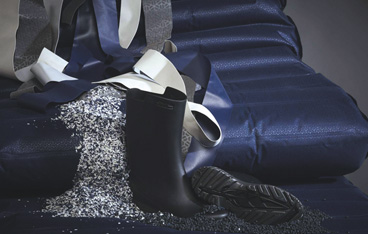
24.11.2023
Матрасы из ПВХ превращаются в сабо
Французский производитель спорттоваров Decathlon в настоящее время ушел из России, хотя на ряде маркетплейсов еще можно найти товары этого бренда. Однако кейс, о котором рассказывается в интервью, интересен как пример успешного апсайклинг-проекта, реализованного в достаточно узкой нише. О подробностях рассказывают Филипп Грессье, директор по продажам компании Benvic, специализирующейся на изготовлении компаундов,
и Лена Дефонтен, инженер-материаловед, ответственный за разработку и совершенствование термопластичных материалов с тканевым покрытием в компании Decathlon.
Выбор изделия и партнера
— Лена, изначально цель компании Decathlon заключалась в том, чтобы наладить рециклинг надувных походных матрасов. Почему вы выбрали именно это изделие?
— Матрасы, ставшие визитной карточкой линейки Quechua camping, —сейчас самый ходовой из наших товаров, изготавливаемых из поливинилхлорида. Годовой объем продаж этих изделий доходит до 2 млн экземпляров. На их производство уходит около 40% от общего количества ПВХ, ежегодно потребляемого нашей компанией. Однако такие матрасы, как и любые другие надувные изделия, могут легко прийти в негодность. Мы провели множество исследований, нацеленных на повышение их прочности, но несмотря на это, последние два-три года уровень возврата поврежденных изделий остается практически неизменным. К сожалению, когда речь идет о продукции из такого узкого ценового сегмента, у нас остается не так много пространства для маневра. Мы практически лишены возможности оказывать услуги по починке подобных товаров в наших мастерских, поскольку цена такого ремонта будет сопоставима со стоимостью нового изделия. Нам показалось недопустимым просто выбрасывать возвращенные матрасы, зная, что большая их часть останется на свалке или же в лучшем случае будет сожжена для выработки электроэнергии. Поэтому в конце 2020 года мы решили найти компанию, которая помогла бы нам устроить более достойное завершение жизненного цикла матрасов путем их вторичной переработки.
— Филипп, представители Decathlon обратились в компанию Benvic?
— Я даже не знаю, кто из нас кого выбрал, но это в конечном счете не важно. Я уверен только в одном: наша встреча была неслучайной. Компания Benvic хорошо известна в качестве специалиста по изготовлению композиций в первую очередь на основе поливинилхлорида. Несмотря на то, что мы также занимаемся и другими термопластичными полимерами, а также биополимерами, в основе нашего бизнеса вот уже более 60 лет лежит компаундирование ПВХ. Более того, начиная с 2019 года, когда нами была куплена компания Ereplast, наша фирма активно выделяет средства на развитие технологии рециклинга данного полимера. Узнав о том, что Decathlon ищет партнеров для изучения возможности осуществления проекта в рамках вторичной переработки матрасов и изготовления обуви, предназначенной для работы в саду и активного отдыха на свежем воздухе, мы увидели в этом отличный шанс извлечь максимум пользы из накопленных нами знаний и опыта.
Решение проблем
— Филипп, вам удалось реализовать проект?
— Думаю да. Мы столкнулись с множеством проблем, требовавших решения. Во-первых, мягкий ПВХ гораздо хуже подходит для вторичной переработки, чем твердый, так как в данном случае используются совсем другие типы пластификаторов, а также вследствие иной степени жесткости материала. Что еще более важно, матрасы компании Decathlon изготавливаются из нескольких материалов. Они на 95% состоят из мягкого поливинилхлорида, при этом одна сторона изделия для большего комфорта покрывается вискозой (4,9% от массы изделия), а клапаны изготавливаются из жесткого ПВХ, АБС и силикона (0,1% от массы изделия). На самом деле, клапаны слишком больших проблем не доставляют, поскольку их можно удалить. К сожалению, данный процесс невозможно автоматизировать — все приходится делать вручную. Главная же техническая сложность была связана с присутствием вискозы.
— Лена, как вы справились с этой проблемой?
— Самый напрашивающийся вариант предполагал отрезание стороны изделия, отделанной вискозой, но в этом случае мы бы теряли 45% материала, пригодного для вторичной переработки. С точки зрения рециклинга такое решение было бы крайне неудовлетворительным. Вискозное покрытие прикрепляется к матрасу при помощи клея, по этой причине удаление его методом отскабливания не представляется возможным. Пытаясь найти способ отделения ПВХ от волокон ткани, мы в том числе изучили возможность использования растворителя. С учетом стоимости ПВХ этот вариант оказался слишком дорогим. Более того, для подобного техпроцесса потребовалось бы большое количество электроэнергии, что связано с серьезными выбросами CO2.
— Филипп, какое решение вы нашли?
— Перебрав все варианты, мы остановились на том, что будем измельчать весь матрас целиком сразу после удаления клапанов. Таким образом, мы получим дробленку ПВХ с примесью вискозы, доля которой будет составлять 4,9%. Несомненно, к принятию данного решения нас подтолкнул наш опыт работы с композициями.
— И каков был результат?
— Первой хорошей новостью стал тот факт, что шредер может с легкостью перерабатывать вискозу, после чего измельченный материал нужно пропустить сквозь пылеуловитель для удаления небольшого количества частиц вискозы. Затем непосредственно перед гранулированием дробленку необходимо отфильтровать для того, чтобы еще раз уменьшить содержание примеси. В конечном итоге какое-то количество вискозы в рецикляте останется, но оно будет невелико.
Однако самое сложное было еще впереди: нам требовалось определиться с параметрами гранул, в которые должен превращаться измельченный материал, включая их размер. Необходимо было грамотно подобрать добавки для того, чтобы обеспечить приемлемую вязкость расплава. И все это нам удалось сделать. Не буду говорить, как именно: это наша профессиональная тайна и мы ревностно ее охраняем. Затем в одном из производственных центров компании Decathlon, расположенном на территории Франции, методом литья под давлением были изготовлены опытные партии сабо. После ряда испытаний производителю удалось добиться ожидаемого результата.
— Лена, эти сабо уже поступили в продажу?
— Пока нет, поскольку мы столкнулись с определенными сложностями. Обратите внимание на то, что сабо изготавливаются из двух элементов: верха и подошвы. В нашем случае в целях гомогенизации дробленки вторичному материалу придается черный цвет. Компания Decathlon предпочла бы иметь возможность изготавливать верх разного цвета, но, к сожалению, это неосуществимо. Кроме того, верхняя часть сабо должна быть чуть более гибкой, чем подошва. Вот почему мы сейчас работаем над созданием нового ПВХ-компаунда. В отдаленной перспективе он сможет прийти на смену эластомерам, традиционно применяемым сейчас производителями сабо. Уже разработанный в рамках проекта вторичный ПВХ-материал планируется использовать для изготовления подошвы, причем скорее всего не только сабо. Мы полагаем, что он прекрасно подойдет для серийного выпуска и других фирменных товаров компании Decathlon, например ботинок.
Возвращаясь к вашему вопросу, могу сказать, что согласно нашим прикидкам новые сабо появятся на полках в 2024 году при условии, что все этапы сертификации данного товара будут успешно пройдены.
Важность проекта и перспективы
— Филипп, проект в самом деле так важен с точки зрения защиты окружающей среды?
— Однозначно! Это ни в коем случае не эксплуатация «зеленой повестки» ради пиара. Прежде всего, обладая полной информацией об источнике вторсырья (его получают исключительно из переработанных матрасов компании Decathlon), мы можем обеспечить максимальную прослеживаемость. Компаундирование осуществляется только на мощностях компании Benvic, а за литье под давлением отвечает Decathlon. Более того, у нас сейчас очень много говорят о реиндустриализации, так вот: новая марка ПВХ разрабатывается, производится и формуется полностью на территории Франции.
В конце концов нам удалось достичь всех целей проекта, то есть обеспечить рециклинг и повторное использование матрасов. Переход с первичного полимера на восстановленный материал позволяет при изготовлении одной пары сабо снизить объем выбросов CO2 как минимум на 10 кг, при этом отпускная цена товара не изменяется. Все это доказывает конкурентоспособность нашего решения.
— Лена, нет ли у вас опасений, что такой источник сырья может быстро иссякнуть?
— Нет. Во время первых испытаний, проходивших во Франции, когда мы перерабатывали только бракованные матрасы, не пытаясь организовать возврат использованных изделий, за 5 месяцев нам удалось собрать около 10 т будущей вторички. Этот факт позволяет нам быть оптимистами в данном вопросе. После того как в январе 2022 года была введена расширенная ответственность производителя (РОП) на товары для спорта и досуга, объемы вторсырья должны только увеличиться. Мы наметили себе цель: собирать 20 т в год. Кроме того, рассматривается возможность организовать рециклинг других фирменных товаров, таких как мячи, изготавливаемые методом ротационного формования, а также различные надувные изделия (каяки, боксерские груши, нарукавники для плавания, спасательные круги и многое другое). Все эти изделия изготавливаются из ПВХ очень похожих марок. Таким образом, источник вторсырья будет постепенно пополняться. Резюмируя, можно сказать, что, несмотря на то, что ПВХ имеет спорную репутацию, этот полимер хорошо подходит для вторичной переработки — как жесткие, так и гибкие его разновидности. Разница заключается только в том, что для организации рециклинга последних требуется немного больше усилий, изобретательности и мастерства. При этом данная задача является вполне выполнимой, что мы и продемонстрировали на примере матрасов.
— Этот проект кажется весьма успешным. Филипп, помог ли он открыть новые перспективы для компании Benvic?
— Недавно к нам обратился производитель обуви и попросил помочь ему с изготовлением подошв из восстановленного ПВХ. Стоит отметить, что, с тех пор как стартовал наш проект с Decathlon, мы стали большими специалистами в данной области. Наша компания также разрабатывает технологию рециклинга широко используемых дорожных оранжевых конусов. Еще мы задумываемся о вторичной переработке больничных отходов.
Посмотреть в журнале
и Лена Дефонтен, инженер-материаловед, ответственный за разработку и совершенствование термопластичных материалов с тканевым покрытием в компании Decathlon.
Выбор изделия и партнера
— Лена, изначально цель компании Decathlon заключалась в том, чтобы наладить рециклинг надувных походных матрасов. Почему вы выбрали именно это изделие?
— Матрасы, ставшие визитной карточкой линейки Quechua camping, —сейчас самый ходовой из наших товаров, изготавливаемых из поливинилхлорида. Годовой объем продаж этих изделий доходит до 2 млн экземпляров. На их производство уходит около 40% от общего количества ПВХ, ежегодно потребляемого нашей компанией. Однако такие матрасы, как и любые другие надувные изделия, могут легко прийти в негодность. Мы провели множество исследований, нацеленных на повышение их прочности, но несмотря на это, последние два-три года уровень возврата поврежденных изделий остается практически неизменным. К сожалению, когда речь идет о продукции из такого узкого ценового сегмента, у нас остается не так много пространства для маневра. Мы практически лишены возможности оказывать услуги по починке подобных товаров в наших мастерских, поскольку цена такого ремонта будет сопоставима со стоимостью нового изделия. Нам показалось недопустимым просто выбрасывать возвращенные матрасы, зная, что большая их часть останется на свалке или же в лучшем случае будет сожжена для выработки электроэнергии. Поэтому в конце 2020 года мы решили найти компанию, которая помогла бы нам устроить более достойное завершение жизненного цикла матрасов путем их вторичной переработки.
— Филипп, представители Decathlon обратились в компанию Benvic?
— Я даже не знаю, кто из нас кого выбрал, но это в конечном счете не важно. Я уверен только в одном: наша встреча была неслучайной. Компания Benvic хорошо известна в качестве специалиста по изготовлению композиций в первую очередь на основе поливинилхлорида. Несмотря на то, что мы также занимаемся и другими термопластичными полимерами, а также биополимерами, в основе нашего бизнеса вот уже более 60 лет лежит компаундирование ПВХ. Более того, начиная с 2019 года, когда нами была куплена компания Ereplast, наша фирма активно выделяет средства на развитие технологии рециклинга данного полимера. Узнав о том, что Decathlon ищет партнеров для изучения возможности осуществления проекта в рамках вторичной переработки матрасов и изготовления обуви, предназначенной для работы в саду и активного отдыха на свежем воздухе, мы увидели в этом отличный шанс извлечь максимум пользы из накопленных нами знаний и опыта.
Решение проблем
— Филипп, вам удалось реализовать проект?
— Думаю да. Мы столкнулись с множеством проблем, требовавших решения. Во-первых, мягкий ПВХ гораздо хуже подходит для вторичной переработки, чем твердый, так как в данном случае используются совсем другие типы пластификаторов, а также вследствие иной степени жесткости материала. Что еще более важно, матрасы компании Decathlon изготавливаются из нескольких материалов. Они на 95% состоят из мягкого поливинилхлорида, при этом одна сторона изделия для большего комфорта покрывается вискозой (4,9% от массы изделия), а клапаны изготавливаются из жесткого ПВХ, АБС и силикона (0,1% от массы изделия). На самом деле, клапаны слишком больших проблем не доставляют, поскольку их можно удалить. К сожалению, данный процесс невозможно автоматизировать — все приходится делать вручную. Главная же техническая сложность была связана с присутствием вискозы.
— Лена, как вы справились с этой проблемой?
— Самый напрашивающийся вариант предполагал отрезание стороны изделия, отделанной вискозой, но в этом случае мы бы теряли 45% материала, пригодного для вторичной переработки. С точки зрения рециклинга такое решение было бы крайне неудовлетворительным. Вискозное покрытие прикрепляется к матрасу при помощи клея, по этой причине удаление его методом отскабливания не представляется возможным. Пытаясь найти способ отделения ПВХ от волокон ткани, мы в том числе изучили возможность использования растворителя. С учетом стоимости ПВХ этот вариант оказался слишком дорогим. Более того, для подобного техпроцесса потребовалось бы большое количество электроэнергии, что связано с серьезными выбросами CO2.
— Филипп, какое решение вы нашли?
— Перебрав все варианты, мы остановились на том, что будем измельчать весь матрас целиком сразу после удаления клапанов. Таким образом, мы получим дробленку ПВХ с примесью вискозы, доля которой будет составлять 4,9%. Несомненно, к принятию данного решения нас подтолкнул наш опыт работы с композициями.
— И каков был результат?
— Первой хорошей новостью стал тот факт, что шредер может с легкостью перерабатывать вискозу, после чего измельченный материал нужно пропустить сквозь пылеуловитель для удаления небольшого количества частиц вискозы. Затем непосредственно перед гранулированием дробленку необходимо отфильтровать для того, чтобы еще раз уменьшить содержание примеси. В конечном итоге какое-то количество вискозы в рецикляте останется, но оно будет невелико.
Однако самое сложное было еще впереди: нам требовалось определиться с параметрами гранул, в которые должен превращаться измельченный материал, включая их размер. Необходимо было грамотно подобрать добавки для того, чтобы обеспечить приемлемую вязкость расплава. И все это нам удалось сделать. Не буду говорить, как именно: это наша профессиональная тайна и мы ревностно ее охраняем. Затем в одном из производственных центров компании Decathlon, расположенном на территории Франции, методом литья под давлением были изготовлены опытные партии сабо. После ряда испытаний производителю удалось добиться ожидаемого результата.
— Лена, эти сабо уже поступили в продажу?
— Пока нет, поскольку мы столкнулись с определенными сложностями. Обратите внимание на то, что сабо изготавливаются из двух элементов: верха и подошвы. В нашем случае в целях гомогенизации дробленки вторичному материалу придается черный цвет. Компания Decathlon предпочла бы иметь возможность изготавливать верх разного цвета, но, к сожалению, это неосуществимо. Кроме того, верхняя часть сабо должна быть чуть более гибкой, чем подошва. Вот почему мы сейчас работаем над созданием нового ПВХ-компаунда. В отдаленной перспективе он сможет прийти на смену эластомерам, традиционно применяемым сейчас производителями сабо. Уже разработанный в рамках проекта вторичный ПВХ-материал планируется использовать для изготовления подошвы, причем скорее всего не только сабо. Мы полагаем, что он прекрасно подойдет для серийного выпуска и других фирменных товаров компании Decathlon, например ботинок.
Возвращаясь к вашему вопросу, могу сказать, что согласно нашим прикидкам новые сабо появятся на полках в 2024 году при условии, что все этапы сертификации данного товара будут успешно пройдены.
Важность проекта и перспективы
— Филипп, проект в самом деле так важен с точки зрения защиты окружающей среды?
— Однозначно! Это ни в коем случае не эксплуатация «зеленой повестки» ради пиара. Прежде всего, обладая полной информацией об источнике вторсырья (его получают исключительно из переработанных матрасов компании Decathlon), мы можем обеспечить максимальную прослеживаемость. Компаундирование осуществляется только на мощностях компании Benvic, а за литье под давлением отвечает Decathlon. Более того, у нас сейчас очень много говорят о реиндустриализации, так вот: новая марка ПВХ разрабатывается, производится и формуется полностью на территории Франции.
В конце концов нам удалось достичь всех целей проекта, то есть обеспечить рециклинг и повторное использование матрасов. Переход с первичного полимера на восстановленный материал позволяет при изготовлении одной пары сабо снизить объем выбросов CO2 как минимум на 10 кг, при этом отпускная цена товара не изменяется. Все это доказывает конкурентоспособность нашего решения.
— Лена, нет ли у вас опасений, что такой источник сырья может быстро иссякнуть?
— Нет. Во время первых испытаний, проходивших во Франции, когда мы перерабатывали только бракованные матрасы, не пытаясь организовать возврат использованных изделий, за 5 месяцев нам удалось собрать около 10 т будущей вторички. Этот факт позволяет нам быть оптимистами в данном вопросе. После того как в январе 2022 года была введена расширенная ответственность производителя (РОП) на товары для спорта и досуга, объемы вторсырья должны только увеличиться. Мы наметили себе цель: собирать 20 т в год. Кроме того, рассматривается возможность организовать рециклинг других фирменных товаров, таких как мячи, изготавливаемые методом ротационного формования, а также различные надувные изделия (каяки, боксерские груши, нарукавники для плавания, спасательные круги и многое другое). Все эти изделия изготавливаются из ПВХ очень похожих марок. Таким образом, источник вторсырья будет постепенно пополняться. Резюмируя, можно сказать, что, несмотря на то, что ПВХ имеет спорную репутацию, этот полимер хорошо подходит для вторичной переработки — как жесткие, так и гибкие его разновидности. Разница заключается только в том, что для организации рециклинга последних требуется немного больше усилий, изобретательности и мастерства. При этом данная задача является вполне выполнимой, что мы и продемонстрировали на примере матрасов.
— Этот проект кажется весьма успешным. Филипп, помог ли он открыть новые перспективы для компании Benvic?
— Недавно к нам обратился производитель обуви и попросил помочь ему с изготовлением подошв из восстановленного ПВХ. Стоит отметить, что, с тех пор как стартовал наш проект с Decathlon, мы стали большими специалистами в данной области. Наша компания также разрабатывает технологию рециклинга широко используемых дорожных оранжевых конусов. Еще мы задумываемся о вторичной переработке больничных отходов.
Посмотреть в журнале