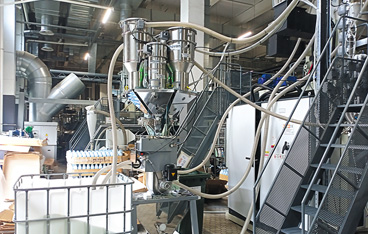
04.03.2024
Периферия на экструзионном производстве
Специалисты компании «БИМ Инжиниринг» («СОЛАН-Д») осуществляют поставку и запуск вспомогательного оборудования в самых разных секторах переработки пластмасс. Одни из последних проектов фирмы — оснащение системой сушки гранулированного сырья линии для экструзии полимерных труб и запуск комплекса оборудования для подачи и дозирования материалов на предприятии, занимающемся выдувом тары.
Трубное производство
Специалисты компании «БИМ Инжиниринг» завершили монтаж периферийного оборудования для экструзионной линии по производству полимерных труб.
Продукция, выпускаемая предприятием-заказчиком, используется в строительстве напорных газовых и водяных трубопроводов. Применение подобных изделий в масштабных проектах возможно только в случае строгого соответствия показателей физико-механических свойств (термостабильности, стойкости к внутреннему гидростатическому давлению и к распространению трещин, усадки после прогрева и других) требованиям изделий ГОСТа.
На параметры выпускаемых труб, в свою очередь, влияют технические характеристики полимерного сырья, поэтому предварительная подготовка материалов — это отдельная стадия технологического процесса, в которой задействовано специальное оборудование.
Заказчик использует гранулированный саженаполненный полиэтилен, являющийся гигроскопичным материалом. В процессе хранения или транспортировки гранулы впитывают влагу, из-за чего при последующей переработке полимера увеличивается пористость поверхности произведенных из него труб и меняются физические свойства изделий — ударная прочность и усадка.
Технологическим решением, которое предложили специалисты фирмы «БИМ Инжиниринг» для осушения полимерных гранул до установленного требованиями ГОСТа значения остаточной влажности 0,01%, стал комплект оборудования, включающий следующие системы:
— сушилка Piovan GMP350 Plus с функцией влагопоглощения;
— сушильный бункер на 10 500 л со встроенным приемником материала;
— трехфазный вакуумный загрузчик F416/3-CF4 для автоматической подачи материала в бункер.
Приемник материала, интегрированный в сушильный бункер, позволяет сохранять уровень тепла в установке и повышает энергоэффективность оборудования.
Комплектация Plus в сушилках серии GMP подразумевает наличие встроенной функции экономии электроэнергии, что позволяет снижать себестоимость продукции без потери ее качества. В стандартных сушилках воздуходувка всегда работает на максимальную мощность, независимо от того, требуется ли такой расход воздуха для просушки материала согласно рекомендациям производителя сырья. В версии Piovan GMP Plus экономия потребляемой электроэнергии достигается благодаря настройке требуемой производительности воздуходувки. За счет сокращения расхода воздуха уменьшается и потребление электроэнергии нагревателем.
Пульт управления процессом сушки — это 7-дюймовый цветной сенсорный экран с удобным интерфейсом на русском языке. Для пользователей преду-смотрено несколько уровней доступа в зависимости от уровня их ответственности. С помощью пульта настраиваются и контролируются параметры сушки, такие как температурный режим, точка росы, уровень загрузки бункера и другие.
В процессе реализации проекта перед инженерами фирмы «БИМ Инжиниринг» стояла сложная задача по размещению крупногабаритного оборудования на втором ярусе производственного цеха, где пространство ограничено элементами строительной конструкции. Высота бункера вместе с загрузчиком — 7 метров, а вес — более 2 т. Специалистам потребовалось снять его с горизонтальной транспортировочной платформы и закрепить в вертикальном положении на металлическом парапете высотой 3,3 м. После завершения монтажа оборудование было подключено к одной из действующих экструзионных линий, произведен запуск и успешный вывод сушилки на рабочий режим.
Данный проект является частью большого цикла проектов, реализуемых компанией «БИМ Инжиниринг» в сегменте производства полимерных труб. Активный рост этого направления в 2023 году сформировал высокий спрос на грамотные эффективные инженерные решения по оснащению и модернизации предприятий отрасли периферийным оборудованием.
Экструзионный выдув тары
На крупном российском предприятии, выпускающем средства бытовой и профессиональной химии, сотрудниками фирмы «БИМ Инжиниринг» завершен очередной этап оснащения периферийным оборудованием цеха по производству тары методом экструзионно-выдувного формования.
Четыре экструзионно-выдувные машины Magic, приобретенные заказчиком, предназначены для изготовления 3-слойных полиэтиленовых канистр различного объема. Компоненты для внутреннего и внешнего слоя изделия дозируются с помощью двухобъемных дозаторов MDP2 (Piovan) с одной и двумя дозирующими станциями и накопительными бункерами объемом 20 л. Дозаторы установлены на горловины экструдеров и укомплектованы тахоприводами для регулировки работы дозаторов в зависимости от изменения скорости вращения шнеков экструдеров. Дозирующие станции оснащены приемниками материала, вместимостью от 5 до 50 л.
Весовые гравиметрические дозаторы Quantum Q50 обеспечивают подготовку сырья для среднего слоя выпускаемого изделия. Каждый Quantum Q50 имеет пять дозирующих станций с приемниками материалов, благодаря чему заказчик может использовать в рецептурах до пяти различных компонентов. Дозаторы оснащены цветными сенсорными 10-дюймовыми дисплеями с интерфейсом на русском языке.
Процесс загрузки организован с помощью централизованной системы подачи сырья. Основной материал (ПЭНД) поступает ко всем потребителям напрямую из силоса. За транспортировку компонентов по трубопроводам отвечают трехфазные вакуумные загрузчики серии F (Piovan).
Контроль и управление параметрами загрузки происходит с помощью системы Easy3 (Piovan). Графический дисплей Easy3 позволяет визуализировать текущее состояние каждой единицы оборудования и настраивать режимы работы приемников материала и трехфазных вакуумных загрузчиков.
Особенностью процесса экструзионно-выдувного формования является образование большого количества облоя. В данном же проекте реализован процесс замкнутого цикла. Облой с помощью ленточного конвейера N-CPR поступает в дробилку для измельчения. Полученная дробленка через циклонный фильтр попадает в резидентный бункер, из которого непрерывно (инлайн) добавляется к основному материалу.
Конвейеры оснащены пластинчатыми металлодетекторами, способными выявить включения размером до 0,3 мм. Металлодетекторы помогают предотвратить попадание примесей в расплав полимера, что может привести к браку продукции и поломке оборудования.
Реализованное решение является оптимальным для выполнения задачи, поставленной заказчиком. Это уже восьмой проект, запущенный на данном предприятии в сотрудничестве с компанией.
Посмотреть в журнале
Трубное производство
Специалисты компании «БИМ Инжиниринг» завершили монтаж периферийного оборудования для экструзионной линии по производству полимерных труб.
Продукция, выпускаемая предприятием-заказчиком, используется в строительстве напорных газовых и водяных трубопроводов. Применение подобных изделий в масштабных проектах возможно только в случае строгого соответствия показателей физико-механических свойств (термостабильности, стойкости к внутреннему гидростатическому давлению и к распространению трещин, усадки после прогрева и других) требованиям изделий ГОСТа.
На параметры выпускаемых труб, в свою очередь, влияют технические характеристики полимерного сырья, поэтому предварительная подготовка материалов — это отдельная стадия технологического процесса, в которой задействовано специальное оборудование.
Заказчик использует гранулированный саженаполненный полиэтилен, являющийся гигроскопичным материалом. В процессе хранения или транспортировки гранулы впитывают влагу, из-за чего при последующей переработке полимера увеличивается пористость поверхности произведенных из него труб и меняются физические свойства изделий — ударная прочность и усадка.
Технологическим решением, которое предложили специалисты фирмы «БИМ Инжиниринг» для осушения полимерных гранул до установленного требованиями ГОСТа значения остаточной влажности 0,01%, стал комплект оборудования, включающий следующие системы:
— сушилка Piovan GMP350 Plus с функцией влагопоглощения;
— сушильный бункер на 10 500 л со встроенным приемником материала;
— трехфазный вакуумный загрузчик F416/3-CF4 для автоматической подачи материала в бункер.
Приемник материала, интегрированный в сушильный бункер, позволяет сохранять уровень тепла в установке и повышает энергоэффективность оборудования.
Комплектация Plus в сушилках серии GMP подразумевает наличие встроенной функции экономии электроэнергии, что позволяет снижать себестоимость продукции без потери ее качества. В стандартных сушилках воздуходувка всегда работает на максимальную мощность, независимо от того, требуется ли такой расход воздуха для просушки материала согласно рекомендациям производителя сырья. В версии Piovan GMP Plus экономия потребляемой электроэнергии достигается благодаря настройке требуемой производительности воздуходувки. За счет сокращения расхода воздуха уменьшается и потребление электроэнергии нагревателем.
Пульт управления процессом сушки — это 7-дюймовый цветной сенсорный экран с удобным интерфейсом на русском языке. Для пользователей преду-смотрено несколько уровней доступа в зависимости от уровня их ответственности. С помощью пульта настраиваются и контролируются параметры сушки, такие как температурный режим, точка росы, уровень загрузки бункера и другие.
В процессе реализации проекта перед инженерами фирмы «БИМ Инжиниринг» стояла сложная задача по размещению крупногабаритного оборудования на втором ярусе производственного цеха, где пространство ограничено элементами строительной конструкции. Высота бункера вместе с загрузчиком — 7 метров, а вес — более 2 т. Специалистам потребовалось снять его с горизонтальной транспортировочной платформы и закрепить в вертикальном положении на металлическом парапете высотой 3,3 м. После завершения монтажа оборудование было подключено к одной из действующих экструзионных линий, произведен запуск и успешный вывод сушилки на рабочий режим.
Данный проект является частью большого цикла проектов, реализуемых компанией «БИМ Инжиниринг» в сегменте производства полимерных труб. Активный рост этого направления в 2023 году сформировал высокий спрос на грамотные эффективные инженерные решения по оснащению и модернизации предприятий отрасли периферийным оборудованием.
Экструзионный выдув тары
На крупном российском предприятии, выпускающем средства бытовой и профессиональной химии, сотрудниками фирмы «БИМ Инжиниринг» завершен очередной этап оснащения периферийным оборудованием цеха по производству тары методом экструзионно-выдувного формования.
Четыре экструзионно-выдувные машины Magic, приобретенные заказчиком, предназначены для изготовления 3-слойных полиэтиленовых канистр различного объема. Компоненты для внутреннего и внешнего слоя изделия дозируются с помощью двухобъемных дозаторов MDP2 (Piovan) с одной и двумя дозирующими станциями и накопительными бункерами объемом 20 л. Дозаторы установлены на горловины экструдеров и укомплектованы тахоприводами для регулировки работы дозаторов в зависимости от изменения скорости вращения шнеков экструдеров. Дозирующие станции оснащены приемниками материала, вместимостью от 5 до 50 л.
Весовые гравиметрические дозаторы Quantum Q50 обеспечивают подготовку сырья для среднего слоя выпускаемого изделия. Каждый Quantum Q50 имеет пять дозирующих станций с приемниками материалов, благодаря чему заказчик может использовать в рецептурах до пяти различных компонентов. Дозаторы оснащены цветными сенсорными 10-дюймовыми дисплеями с интерфейсом на русском языке.
Процесс загрузки организован с помощью централизованной системы подачи сырья. Основной материал (ПЭНД) поступает ко всем потребителям напрямую из силоса. За транспортировку компонентов по трубопроводам отвечают трехфазные вакуумные загрузчики серии F (Piovan).
Контроль и управление параметрами загрузки происходит с помощью системы Easy3 (Piovan). Графический дисплей Easy3 позволяет визуализировать текущее состояние каждой единицы оборудования и настраивать режимы работы приемников материала и трехфазных вакуумных загрузчиков.
Особенностью процесса экструзионно-выдувного формования является образование большого количества облоя. В данном же проекте реализован процесс замкнутого цикла. Облой с помощью ленточного конвейера N-CPR поступает в дробилку для измельчения. Полученная дробленка через циклонный фильтр попадает в резидентный бункер, из которого непрерывно (инлайн) добавляется к основному материалу.
Конвейеры оснащены пластинчатыми металлодетекторами, способными выявить включения размером до 0,3 мм. Металлодетекторы помогают предотвратить попадание примесей в расплав полимера, что может привести к браку продукции и поломке оборудования.
Реализованное решение является оптимальным для выполнения задачи, поставленной заказчиком. Это уже восьмой проект, запущенный на данном предприятии в сотрудничестве с компанией.
Посмотреть в журнале