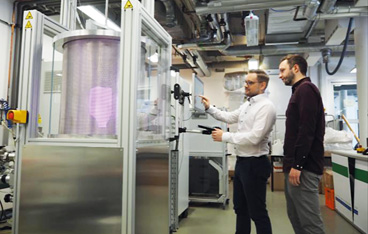
04.10.2023
Плазменное осаждение барьерных покрытий
Для многих изделий, чувствительных к внешнему воздействию или же, наоборот, представляющих опасность, требуется адекватная защитная упаковка, обладающая высокими барьерными свойствами. Для этого используются выдувные пластиковые емкости, изготавливаемые из нескольких материалов или фторированных полимеров. В первом случае дешевые пластики комбинируются с дорогими барьерными марками, что делает рециклинг подобных емкостей весьма проблематичным. Во втором в результате фторирования образуются пер- и полифторалкильные соединения (ПФАС), которые относят к так называемым вечным химикатам, не разлагающимся в природе. Однако сегодня технология плазменного осаждения барьерных покрытий, не содержащих фтора, на поверхность бутылок и канистр позволяет сделать их полностью пригодными к рециклингу.
В недавнем исследовании, проводившемся американским Агентством по защите окружающей среды (Environmental Protection Agency — EPA) и посвященном особенностям использования емкостей из фторированного полиэтилена высокой плотности (ПЭВП), было показано, что при хранении в них пестицидов или другой продукции в жидкой форме, она с высокой долей вероятности будет загрязнена пер- и полифторалкильными соединениями. Из этого был сделан вывод о том, что в конечном итоге ПФАС неизбежно попадает в окружающую среду и непосредственно в тело человека.
В Стратегии по грамотному использованию химикатов (Chemicals Strategy for Sustainability — CSS), утвержденной ЕС в рамках «Европейского зеленого курса» и призванной защитить окружающую среду от токсичных веществ, ПФАС уделяется особое внимание в связи с наличием многочисленных случаев загрязнения природы. Голландский Национальный институт здравоохранения и окружающей среды (RIVM) выступил с инициативой ограничить использование всех видов пер- и полифторалкильных соединений. Европа стремится наложить запрет на применение ПФАС за исключением случаев, когда такие вещества признаются незаменимыми: это прописано в стратегии CSS, того же требуют и Европейский парламент, и Евросовет. Под незаменимостью понимается, например, невозможность подобрать более безопасную альтернативу.
В этой связи специалисты IonKraft — дочернего подразделения Института переработки пластмасс (Institut fuer Kunststoffverarbeitung in Industrie und Handwerk — IKV), являющегося частью Рейнско-Вестфальского технического университета Ахена (Rheinisch-Westfaelische Technische Hochschule Aachen), — разработали систему нанесения барьерных покрытий на основе силикона, которые по своим защитным функциям не отличаются ни от многослойной упаковки, состоящей из нескольких материалов, ни от решений, основанных на фторировании полимера. Контейнер нового типа остается полностью пригодным для рециклинга, поскольку толщина такого покрытия составляет менее 100 нм. Новая технология обеспечивает преграду для проникновения газа, растворов и водяного пара, а также защищает от агрессивных разъедающих веществ. Покрытие не представляет угрозы при контакте с продуктами питания и может быть нанесено на любой пластик.
Что такое плазма?
Плазма — это одно из четырех классических агрегатных состояний вещества. Она содержит значительное количество свободно перемещающихся заряженных частиц, и поэтому обычно описывается как ионизированный газ. Свойства плазмы преимущественно определяются взаимодействием заряженных частиц. Постоянные неупругие и упругие столкновения между ними могут привести к усилению ионизационных процессов. Если возбудить плазму при помощи определенных видов так называемых мономерных газов, такие процессы приведут к появлению реактивных частиц, которые могут быть адсорбированы на поверхность с формированием покрытия. Процесс нанесения покрытий с использованием плазмы получил название «плазменная полимеризация» или «плазмохимическое газофазное осаждение» (ПХГФО).
Плазмохимическое газофазное осаждение
Пластики производятся путем обычной полимеризации, представляющей собой химический процесс, в ходе которого мономеры связываются вместе, формируя длинные молекулярные цепочки (полимеры). С другой стороны, при плазмохимическом газофазном осаждении происходит полимеризация фрагментов, сформированных в плазме, в результате чего из мономерного газа образуются полимерные структуры, состоящие частично из старых, а частично из новых функциональных групп. Такие фрагменты молекул могут рекомбинироваться в плазме, а затем адсорбироваться на поверхность подложки, образуя покрытие.
Свойства покрытия очень сильно зависят от параметров техпроцесса, а именно от используемой смеси газов и их массового расхода, от энергетической плотности плазмы, от давления и от длительности процесса нанесения покрытия.
Для нанесения покрытия на подложки, чувствительные к высокой температуре (например, на пластики), может использоваться только низкотемпературная плазма. Один из способов ее получения связан с воспламенением плазмы в условиях низкого давления, обычно ограниченного несколькими Па. В результате рабочая температура техпроцесса лишь слегка превышает комнатную из-за увеличившейся средней длины свободного пробега частиц газа вне зависимости от того, какой именно газ используется.
Для формирования плазмы специалисты IonKraft используют метод микроволнового возбуждения, поскольку он позволяет добиться особенно высокой скорости оседания частиц.
Технология от IonKraft
На рис. 1 отражены некоторые важнейшие данные, свидетельствующие об эффективности технологии от IonKraft. В приведенных примерах покрытия наносились на бутылки из ПЭВП емкостью 1 л.
Под кислородопроницаемостью понимается постоянная скорость, с которой соответствующий газ проникает сквозь подложку при определенных значениях температуры и относительной влажности. Данный показатель является важнейшим индикатором барьерных свойств покрытия применительно к газам. График, изображенный на рис. 2, демонстрирует результаты эталонных измерений, в ходе которых сравнивались уровни кислородопроницаемости у бутылок из ПЭВП, получивших покрытие по методу, разработанному IonKraft, у ПЭВП-бутылок, оставленных без покрытия, и у многослойных изделий, в которых в качестве барьерного пластика используется полиамид (ПА) либо сополимер этилена и винилового спирта (СЭВС).
Одним из важнейших моментов, способствующих широкому применению барьерной технологии от IonKraft, является химическая стойкость покрытия к воздействию агрессивной среды.
Для того чтобы продемонстрировать сопротивляемость к химическому воздействию, было проведено испытание с использованием гидроксида натрия NaOH (pH=13) в качестве агрессивной жидкости. Литровые бутылки из ПЭВП получили инновационное покрытие, после чего были измерены их барьерные свойства против кислорода. На следующей стадии эксперимента эти бутылки были наполнены едким гидроксидом натрия, а потом отправлены на склад, где хранились в течение 4 недель при температуре 40°C. Результаты повторного измерения уровня кислородопроницаемости показали, что он изменился очень незначительно. Это однозначно свидетельствует об устойчивости нанесенного покрытия.
Защита от растворителей
Важнейшим индикатором, свидетельствующем об эффективности защиты изделия от растворителей, является измерение фактической убыли хранящейся жидкости в связи с миграцией, осуществляемое гравиметрическим способом. Специалисты IonKraft осуществили проверку разработанной ими технологии нанесения покрытий совместно с компаниями-партнерами в соответствии с правилами испытания упаковки, установленными европейским Соглашением о международной дорожной перевозке опасных грузов (ДОПОГ). Согласно данному нормативному акту требуется в обязательном порядке проводить тест на газопроницаемость емкостей, предназначенных для хранения жидкостей с точкой возгорания менее <61°C (например, таких растворителей, как бензол, толуол или ксилол). В ходе таких испытаний в сосуд заливается либо оригинальное изделие клиента, либо стандартная жидкая углеводородная смесь (уайт-спирит), после чего он должен храниться в течение 28 дней при температуре 23°C и относительной влажности 50%. Газопроницаемость определяется гравиметрическим способом, как указано на рис. 3. Ее значение не должно превышать 0,008 г/(л∙ч).
Тем не менее многие компании предъявляют повышенные требования к барьерным свойствам используемых емкостей, которые должны выдерживать более высокую температуру хранения и обеспечивать меньший уровень миграции в течение аналогичного или же более длительного периода времени. Для того чтобы продемонстрировать эффективность своего покрытия, подразделение IonKraft провело испытания с применением различных жидкостей при температуре хранения 40°C. Их результаты указаны на графике, представленном на рис. 4. Они позволяют убедиться в том, что новая технология обеспечивает высокие барьерные свойства против всех использованных жидкостей. В случае с уайт-спиритом (соединение, рекомендованное ДОПОГ в качестве стандартного растворителя) уровень газопроницаемости тестового образца составил примерно 0,0000298 г/(л∙ч), что гораздо ниже предписываемого ЕС показателя.
Производственное оборудование
Помимо экспериментов, проводившихся вместе с партнерами из химических и упаковочных компаний для подтверждения эффективности своей разработки, специалисты из IonKraft также создали прототип системы нанесения покрытий, который рассчитан на обработку емкостей различной формы вместимостью от одного до двадцати литров.
Более того, скооперировавшись с одним из партнеров, подразделение IonKraft разработало автоматическую систему, предназначенную для непрерывного нанесения покрытий в составе промышленных линий для выдувного формования. При этом предусмотрена возможность обеспечивать любой требуемый уровень производительности линии путем встраивания в нее необходимого количества специализированных модулей.
В 2023 году подразделение IonKraft планирует построить совместно с партнером, специализирующемся на создании машин и средств автоматизации, первую линию, способную обеспечить нанесение покрытий в промышленных масштабах. После чего, с целью подтвердить надежность и долговременную эффективность барьерного покрытия, создаваемого при помощи нового техпроцесса, планируется наладить опытное производство на предприятии поставщика упаковки. Первые коммерческие партии таких машин поступят на рынок в 2024 году.
Посмотреть в журнале
В недавнем исследовании, проводившемся американским Агентством по защите окружающей среды (Environmental Protection Agency — EPA) и посвященном особенностям использования емкостей из фторированного полиэтилена высокой плотности (ПЭВП), было показано, что при хранении в них пестицидов или другой продукции в жидкой форме, она с высокой долей вероятности будет загрязнена пер- и полифторалкильными соединениями. Из этого был сделан вывод о том, что в конечном итоге ПФАС неизбежно попадает в окружающую среду и непосредственно в тело человека.
В Стратегии по грамотному использованию химикатов (Chemicals Strategy for Sustainability — CSS), утвержденной ЕС в рамках «Европейского зеленого курса» и призванной защитить окружающую среду от токсичных веществ, ПФАС уделяется особое внимание в связи с наличием многочисленных случаев загрязнения природы. Голландский Национальный институт здравоохранения и окружающей среды (RIVM) выступил с инициативой ограничить использование всех видов пер- и полифторалкильных соединений. Европа стремится наложить запрет на применение ПФАС за исключением случаев, когда такие вещества признаются незаменимыми: это прописано в стратегии CSS, того же требуют и Европейский парламент, и Евросовет. Под незаменимостью понимается, например, невозможность подобрать более безопасную альтернативу.
В этой связи специалисты IonKraft — дочернего подразделения Института переработки пластмасс (Institut fuer Kunststoffverarbeitung in Industrie und Handwerk — IKV), являющегося частью Рейнско-Вестфальского технического университета Ахена (Rheinisch-Westfaelische Technische Hochschule Aachen), — разработали систему нанесения барьерных покрытий на основе силикона, которые по своим защитным функциям не отличаются ни от многослойной упаковки, состоящей из нескольких материалов, ни от решений, основанных на фторировании полимера. Контейнер нового типа остается полностью пригодным для рециклинга, поскольку толщина такого покрытия составляет менее 100 нм. Новая технология обеспечивает преграду для проникновения газа, растворов и водяного пара, а также защищает от агрессивных разъедающих веществ. Покрытие не представляет угрозы при контакте с продуктами питания и может быть нанесено на любой пластик.
Что такое плазма?
Плазма — это одно из четырех классических агрегатных состояний вещества. Она содержит значительное количество свободно перемещающихся заряженных частиц, и поэтому обычно описывается как ионизированный газ. Свойства плазмы преимущественно определяются взаимодействием заряженных частиц. Постоянные неупругие и упругие столкновения между ними могут привести к усилению ионизационных процессов. Если возбудить плазму при помощи определенных видов так называемых мономерных газов, такие процессы приведут к появлению реактивных частиц, которые могут быть адсорбированы на поверхность с формированием покрытия. Процесс нанесения покрытий с использованием плазмы получил название «плазменная полимеризация» или «плазмохимическое газофазное осаждение» (ПХГФО).
Плазмохимическое газофазное осаждение
Пластики производятся путем обычной полимеризации, представляющей собой химический процесс, в ходе которого мономеры связываются вместе, формируя длинные молекулярные цепочки (полимеры). С другой стороны, при плазмохимическом газофазном осаждении происходит полимеризация фрагментов, сформированных в плазме, в результате чего из мономерного газа образуются полимерные структуры, состоящие частично из старых, а частично из новых функциональных групп. Такие фрагменты молекул могут рекомбинироваться в плазме, а затем адсорбироваться на поверхность подложки, образуя покрытие.
Свойства покрытия очень сильно зависят от параметров техпроцесса, а именно от используемой смеси газов и их массового расхода, от энергетической плотности плазмы, от давления и от длительности процесса нанесения покрытия.
Для нанесения покрытия на подложки, чувствительные к высокой температуре (например, на пластики), может использоваться только низкотемпературная плазма. Один из способов ее получения связан с воспламенением плазмы в условиях низкого давления, обычно ограниченного несколькими Па. В результате рабочая температура техпроцесса лишь слегка превышает комнатную из-за увеличившейся средней длины свободного пробега частиц газа вне зависимости от того, какой именно газ используется.
Для формирования плазмы специалисты IonKraft используют метод микроволнового возбуждения, поскольку он позволяет добиться особенно высокой скорости оседания частиц.
Технология от IonKraft
На рис. 1 отражены некоторые важнейшие данные, свидетельствующие об эффективности технологии от IonKraft. В приведенных примерах покрытия наносились на бутылки из ПЭВП емкостью 1 л.
Под кислородопроницаемостью понимается постоянная скорость, с которой соответствующий газ проникает сквозь подложку при определенных значениях температуры и относительной влажности. Данный показатель является важнейшим индикатором барьерных свойств покрытия применительно к газам. График, изображенный на рис. 2, демонстрирует результаты эталонных измерений, в ходе которых сравнивались уровни кислородопроницаемости у бутылок из ПЭВП, получивших покрытие по методу, разработанному IonKraft, у ПЭВП-бутылок, оставленных без покрытия, и у многослойных изделий, в которых в качестве барьерного пластика используется полиамид (ПА) либо сополимер этилена и винилового спирта (СЭВС).
Одним из важнейших моментов, способствующих широкому применению барьерной технологии от IonKraft, является химическая стойкость покрытия к воздействию агрессивной среды.
Для того чтобы продемонстрировать сопротивляемость к химическому воздействию, было проведено испытание с использованием гидроксида натрия NaOH (pH=13) в качестве агрессивной жидкости. Литровые бутылки из ПЭВП получили инновационное покрытие, после чего были измерены их барьерные свойства против кислорода. На следующей стадии эксперимента эти бутылки были наполнены едким гидроксидом натрия, а потом отправлены на склад, где хранились в течение 4 недель при температуре 40°C. Результаты повторного измерения уровня кислородопроницаемости показали, что он изменился очень незначительно. Это однозначно свидетельствует об устойчивости нанесенного покрытия.
Защита от растворителей
Важнейшим индикатором, свидетельствующем об эффективности защиты изделия от растворителей, является измерение фактической убыли хранящейся жидкости в связи с миграцией, осуществляемое гравиметрическим способом. Специалисты IonKraft осуществили проверку разработанной ими технологии нанесения покрытий совместно с компаниями-партнерами в соответствии с правилами испытания упаковки, установленными европейским Соглашением о международной дорожной перевозке опасных грузов (ДОПОГ). Согласно данному нормативному акту требуется в обязательном порядке проводить тест на газопроницаемость емкостей, предназначенных для хранения жидкостей с точкой возгорания менее <61°C (например, таких растворителей, как бензол, толуол или ксилол). В ходе таких испытаний в сосуд заливается либо оригинальное изделие клиента, либо стандартная жидкая углеводородная смесь (уайт-спирит), после чего он должен храниться в течение 28 дней при температуре 23°C и относительной влажности 50%. Газопроницаемость определяется гравиметрическим способом, как указано на рис. 3. Ее значение не должно превышать 0,008 г/(л∙ч).
Тем не менее многие компании предъявляют повышенные требования к барьерным свойствам используемых емкостей, которые должны выдерживать более высокую температуру хранения и обеспечивать меньший уровень миграции в течение аналогичного или же более длительного периода времени. Для того чтобы продемонстрировать эффективность своего покрытия, подразделение IonKraft провело испытания с применением различных жидкостей при температуре хранения 40°C. Их результаты указаны на графике, представленном на рис. 4. Они позволяют убедиться в том, что новая технология обеспечивает высокие барьерные свойства против всех использованных жидкостей. В случае с уайт-спиритом (соединение, рекомендованное ДОПОГ в качестве стандартного растворителя) уровень газопроницаемости тестового образца составил примерно 0,0000298 г/(л∙ч), что гораздо ниже предписываемого ЕС показателя.
Производственное оборудование
Помимо экспериментов, проводившихся вместе с партнерами из химических и упаковочных компаний для подтверждения эффективности своей разработки, специалисты из IonKraft также создали прототип системы нанесения покрытий, который рассчитан на обработку емкостей различной формы вместимостью от одного до двадцати литров.
Более того, скооперировавшись с одним из партнеров, подразделение IonKraft разработало автоматическую систему, предназначенную для непрерывного нанесения покрытий в составе промышленных линий для выдувного формования. При этом предусмотрена возможность обеспечивать любой требуемый уровень производительности линии путем встраивания в нее необходимого количества специализированных модулей.
В 2023 году подразделение IonKraft планирует построить совместно с партнером, специализирующемся на создании машин и средств автоматизации, первую линию, способную обеспечить нанесение покрытий в промышленных масштабах. После чего, с целью подтвердить надежность и долговременную эффективность барьерного покрытия, создаваемого при помощи нового техпроцесса, планируется наладить опытное производство на предприятии поставщика упаковки. Первые коммерческие партии таких машин поступят на рынок в 2024 году.
Посмотреть в журнале