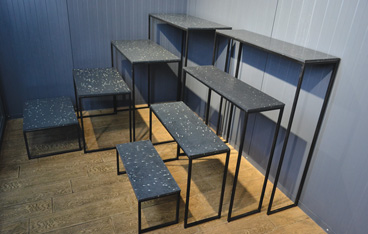
24.01.2024
Творческий стартап в сфере рециклинга
Одним из хитов конференции RePlast, которая прошла 26-27 сентября в Москве, стал доклад Анны и Сергея Ярошевских, основателей стартапа «Реплавим». Семейная пара является участником проекта Торгово-промышленной палаты РФ «Семейные компании России» и более 8 лет развивает свой бизнес в городе Тихорецке Краснодарского края. Первое направление их деятельности — создание большого цветочного кибермаркета, второе — переработка отходов пластмасс методом горячего прессования. В интервью журналу «Пластикс» бизнесмены рассказали, как производят эколисты для создания профессиональной мебели.
Выбор направления
— Анна, как вы с Сергеем пришли к идее запуска стартапа в сфере рециклинга пластмасс?
— Через экопривычки: мы уже более трех лет не выкидываем пластик просто так в мусорку. Сегодня происходит так: купил стаканчик кофе с собой, потом снимаешь крышку с него, вытираешь и кладешь в сумку, чтобы положить дома в контейнер с вторсырьем. Дома мы сортируем все накопленные отходы. В 2022 году поняли, что у нас есть ресурсы для того, чтобы организовать еще один проект и быть полезными обществу. Помощь в переработке отходов — первое, что пришло нам в голову, когда мы задумались о социально полезном бизнесе.
Нам удалось найти проект, который нас вдохновил, потому что мы поняли, что сможем заниматься творчеством и наращивать объемы производства постепенно — это переработка пластика методом горячего прессования. Эта технология используется в проекте PreciousPlastic, созданном Дейвом Хаккенсом. Серия станков и инструментов измельчает, плавит, прессует вторичный пластик, позволяя создавать новые изделия. Отличием переработки пластика методом горячего прессования от других способов является получение неоднородной по цвету поверхности листов, фактурой напоминающей натуральный камень, что открывает широкие возможности для дизайна.
Проект позволяет заинтересованным людям создать свою собственную компанию по переработке отходов, так как все чертежи оборудования и технологии находятся в открытом доступе. Мы воспользовались данной возможностью, чтобы начать перерабатывать вторичный пластик таким методом у нас в России.
— Сергей, какие задачи стояли перед вами, когда вы решили открыть производство?
— Самая первая задача, которая стояла перед нами: найти готовое оборудование с доставкой в Россию. Хотя, конечно, мы мечтаем работать именно на российском оборудовании, так как считаем, что нужно поддерживать сферу отечественного машиностроения, и верим, что у нас это получится.
Когда мы начали поиск, в российских компаниях, связанных с переработкой вторичного пластика, в основном предлагали либо экструдеры, либо оборудование для полимерпесчаного производства. Мы продолжали поиски около месяца, писали запросы на всевозможные сайты в Китае, но подобных прессов там тоже не смогли найти.
Вышли снова на сайт проекта PreciousPlastic и нашли раздел «Базар», где конструкторы со всего мира выставляют свои станки, которые они сделали по доступным для скачивания чертежам, но сложность была в том, что везде высвечивалась фраза «Не доставляется в Россию». И только на самой последней странице мы увидели долгожданную надпись: «Возможна доставка в вашу страну». Сразу позвонили мастеру, и оказалось, что он производит такие станки у нас в Краснодаре, а потом отправляет в Европу, так как в России никто этим не интересовался. Парадокс, конечно.
Практически на следующий день мы выкупили оборудование — измельчитель пластика, горячий пресс, пресс без подогрева (эти станки предназначались для отправки в Чехию, но в то время уже были закрыты границы, поэтому, можно сказать, нам улыбнулась удача).
Купили здание, доукомплектовали линию ЧПУ-станком и инвентарем. Оборудование обошлось нам в 2 млн рублей, плюс около 5,5 млн рублей ушло на приобретение здания и его ремонт, а также на первую закупку сырья и комплектующих. Параллельно писали бизнес-план, анализировали сбытовую нишу, рынок, спрос, предложение.
К производству приступили осенью 2022 года.
— Анна, почему именно мебель?
— Выбор ниши был не случайным. Сейчас такой огромный ассортимент товаров в любой сфере, что создавать 1001-й продукт в линейке таких же — это история уже не про экологию, а про то, что можно перенасыщать рынок до бесконечности, если ты умеешь продавать. Поэтому в первую очередь мы поставили себе задачу создавать что-то узконаправленное, используя уникальные свойства пластика и наших эколистов, создать альтернативу вещам, производство и добыча которых истощают нашу планету.
Решение пришло вместе со спросом. Мы эксперты в цветочном бизнесе, внедряем много собственных разработок в оснащение холодильных витрин — это комплекты стеллажей, столов, стоек. Многие предприниматели в рабочих чатах консультируются с нами по поводу приобретения специальной мебели. После очередного такого запроса мы поняли, что наши эколисты идеально подходят для цветочных холодильников, в которых уровень влажности достигает 90%, а никакой другой материал не выдерживает больше двух лет. Мы полностью сосредоточились на узком направлении — выпуске профессиональной мебели для цветочных салонов (стеллажей в холодильники, для шаров, для упаковки, флористических столов, ресепшен-стоек). Уже сейчас лично у нас спрос на такую профессиональную мебель превышает предложение.
Вторым направлением у нас будет мебель для ванных комнат. Здесь этому материалу тоже нет равных в плане влагостойкости, и эколисты вполне могут стать экологичной заменой натуральному и искусственному камню.
Процесс производства
— Сергей, расскажите подробнее о процессе производства…
— В результате горячего прессования на станках мы получаем листовой материал полностью из вторичного пластика. Как уже говорилось, особенностью такого метода переработки в отличие от экструзии является цвет — он неоднородный, по фактуре напоминает натуральный камень. Можно пробовать самые разные эффекты, смешивать цвета, делать орнаменты. Каждая поверхность получается неповторимой, эксклюзивной.
За время работы мы успели поэкспериментировать: например, перенесли логотип через пакет (просто положили сверху сырья пакет и запекли), делали узоры из крышечек, добивались эффектов мрамора, звездного неба, запекали блестки и мишуру. Работа с цветом в процессе прессования листов — одновременно и преимущество, и недостаток: пластик нельзя окрасить, лист будет таким, какого цвета было сырье, и тут уже возникает проблема для серийного запуска, ведь каждая партия вторичного сырья даже от одних и тех же поставщиков может немного отличаться по оттенку. При этом его может и не быть в нужном количестве. Но в целом при выстраивании партнерства с ответственным производителем вторичной гранулы, думаем, вопрос будет решен.
— Какое сырье используете?
— Бытовой пластик от населения, который мы закупаем в пунктах приема, вторичную гранулу и дробленку. Используем ПЭНД, ПЭВД, реже — полипропилен.
Бытовой пластик (канистры, бутыли, крышки) сначала сортируем по цвету, затем измельчаем в крошку на шредере, и уже дробленый пластик запекаем под прессом. Естественно, при использовании гранулы или дробленки этап досортировки и дробления пропускается. Для увеличения производительности в настоящее время в большей степени используем вторичную гранулу.
— Как, собственно, протекает процесс прессования?
— Первым делом подготавливаем форму. Форма — это два стальных листа, между которыми размещается квадрат со стороной 110 см из профильной трубы нужного размера (1 см, 2 см). Листы обрабатываются литьевой термостойкой смазкой. В форму засыпается пластик: для листа толщиной 1 см понадобится 11 кг сырья, толщиной 2 см — 22 кг. Стальные листы с формой и пластиком помещаются в рабочее поле термопресса, разогретого до 180°C. Под давлением 3-5 т материал выдерживается 1-1,5 ч. За это время пластик подплавляется, смешивается и становится единым листом.
После запекания листу нужно остыть. Для того чтобы термопресс можно было использовать для изготовления следующего изделия, горячая форма перемещается в пресс без подогрева, и пластик находится там еще полтора часа, пока в горячем прессе запекается следующий лист — все должно работать как конвейер.
Но этого времени не хватает, чтобы пластик схватился, из формы его не вытащить, и к тому же при перемещении возможна деформация листа, поэтому для качественных листов нам приходится выдерживать пластик немного дольше под прессом. Таким образом, скорость процесса производства проседает. Если изначально при расчетах мы закладывали 6 листов в смену (12 часов), то по факту мы получаем, что на формирование одного качественного листа на действующем оборудовании уходит около 3 ч, и соответственно в смену можно сделать только 4 листа. Конечно, для полноценного производства это очень мало. Сейчас мы уже не успеваем закрывать заказы с той скоростью, с которой хотелось бы.
Перспективы развития
— Анна, как планируете развиваться дальше?
— Сейчас мы находимся в поиске нового оборудования и новых решений, так как действующие станки имеют очень маленькую производительность и больше подходят для просветительской деятельности (мастер-классов, единичных декоративных изделий). Но нам все-таки хочется развивать этот метод переработки в промышленных масштабах, с возможностью постепенного роста и наращивания объемов.
Пока из компаний, к которым мы обращались по поводу оборудования, ответила только одна. Сейчас мы ведем переговоры с предприятием «Ростполикрафт» по поводу разработки автоматизированной линии по прессованию эколистов, чтобы хоть как-то повысить производительность.
Они предложили разделить два процесса (плавление и прессование) на разные этапы. То есть сначала пластик размещается в печке, подплавляется, и в горячем состоянии форма перемещается на роликах в пресс с водяным охлаждением. Технологию прессования вторичного пластика таким образом мы видели у компании Madera Plastica (Индия). Также при изменении процесса перемещение форм от места к месту происходит полуавтоматически, что также положительно влияет на сокращение длительности процесса. Разделение этапов позволит создать конвейер и ускорит сам процесс: на подплавление пластика понадобится только 45-60 мин, прессование и охлаждение займут столько же времени. Другие плюсы нового решения: будет увеличен размер листов (2×1 м), а производительность увеличится до 20-24 листов в день. Рыночная стоимость квадратного метра листа в размере 3500-4000 рублей будет вполне конкурентоспособной и при этом выгодной для производителя.
— Планируете ли улучшать качественные характеристики листов?
— Да, над тактильными ощущениями и общим видом продукции тоже нужно поработать. Пока нам не удалось добиться глянцевого эффекта: не удается добиться взаимодействия полировочных материалов, паст и смазок с эколистами. А ведь глянцевая поверхность — один из ключевых критериев при покупке мебели населением. Также существует проблема неровностей, пузырей внутри листа.
Будем рады, если с нами свяжутся компании, которые могут помочь советом или делом, и в партнерстве мы сможем серийно получать экоизделия достойного
качества.
Беседовала Анна Виленс
Посмотреть в журнале
Выбор направления
— Анна, как вы с Сергеем пришли к идее запуска стартапа в сфере рециклинга пластмасс?
— Через экопривычки: мы уже более трех лет не выкидываем пластик просто так в мусорку. Сегодня происходит так: купил стаканчик кофе с собой, потом снимаешь крышку с него, вытираешь и кладешь в сумку, чтобы положить дома в контейнер с вторсырьем. Дома мы сортируем все накопленные отходы. В 2022 году поняли, что у нас есть ресурсы для того, чтобы организовать еще один проект и быть полезными обществу. Помощь в переработке отходов — первое, что пришло нам в голову, когда мы задумались о социально полезном бизнесе.
Нам удалось найти проект, который нас вдохновил, потому что мы поняли, что сможем заниматься творчеством и наращивать объемы производства постепенно — это переработка пластика методом горячего прессования. Эта технология используется в проекте PreciousPlastic, созданном Дейвом Хаккенсом. Серия станков и инструментов измельчает, плавит, прессует вторичный пластик, позволяя создавать новые изделия. Отличием переработки пластика методом горячего прессования от других способов является получение неоднородной по цвету поверхности листов, фактурой напоминающей натуральный камень, что открывает широкие возможности для дизайна.
Проект позволяет заинтересованным людям создать свою собственную компанию по переработке отходов, так как все чертежи оборудования и технологии находятся в открытом доступе. Мы воспользовались данной возможностью, чтобы начать перерабатывать вторичный пластик таким методом у нас в России.
— Сергей, какие задачи стояли перед вами, когда вы решили открыть производство?
— Самая первая задача, которая стояла перед нами: найти готовое оборудование с доставкой в Россию. Хотя, конечно, мы мечтаем работать именно на российском оборудовании, так как считаем, что нужно поддерживать сферу отечественного машиностроения, и верим, что у нас это получится.
Когда мы начали поиск, в российских компаниях, связанных с переработкой вторичного пластика, в основном предлагали либо экструдеры, либо оборудование для полимерпесчаного производства. Мы продолжали поиски около месяца, писали запросы на всевозможные сайты в Китае, но подобных прессов там тоже не смогли найти.
Вышли снова на сайт проекта PreciousPlastic и нашли раздел «Базар», где конструкторы со всего мира выставляют свои станки, которые они сделали по доступным для скачивания чертежам, но сложность была в том, что везде высвечивалась фраза «Не доставляется в Россию». И только на самой последней странице мы увидели долгожданную надпись: «Возможна доставка в вашу страну». Сразу позвонили мастеру, и оказалось, что он производит такие станки у нас в Краснодаре, а потом отправляет в Европу, так как в России никто этим не интересовался. Парадокс, конечно.
Практически на следующий день мы выкупили оборудование — измельчитель пластика, горячий пресс, пресс без подогрева (эти станки предназначались для отправки в Чехию, но в то время уже были закрыты границы, поэтому, можно сказать, нам улыбнулась удача).
Купили здание, доукомплектовали линию ЧПУ-станком и инвентарем. Оборудование обошлось нам в 2 млн рублей, плюс около 5,5 млн рублей ушло на приобретение здания и его ремонт, а также на первую закупку сырья и комплектующих. Параллельно писали бизнес-план, анализировали сбытовую нишу, рынок, спрос, предложение.
К производству приступили осенью 2022 года.
— Анна, почему именно мебель?
— Выбор ниши был не случайным. Сейчас такой огромный ассортимент товаров в любой сфере, что создавать 1001-й продукт в линейке таких же — это история уже не про экологию, а про то, что можно перенасыщать рынок до бесконечности, если ты умеешь продавать. Поэтому в первую очередь мы поставили себе задачу создавать что-то узконаправленное, используя уникальные свойства пластика и наших эколистов, создать альтернативу вещам, производство и добыча которых истощают нашу планету.
Решение пришло вместе со спросом. Мы эксперты в цветочном бизнесе, внедряем много собственных разработок в оснащение холодильных витрин — это комплекты стеллажей, столов, стоек. Многие предприниматели в рабочих чатах консультируются с нами по поводу приобретения специальной мебели. После очередного такого запроса мы поняли, что наши эколисты идеально подходят для цветочных холодильников, в которых уровень влажности достигает 90%, а никакой другой материал не выдерживает больше двух лет. Мы полностью сосредоточились на узком направлении — выпуске профессиональной мебели для цветочных салонов (стеллажей в холодильники, для шаров, для упаковки, флористических столов, ресепшен-стоек). Уже сейчас лично у нас спрос на такую профессиональную мебель превышает предложение.
Вторым направлением у нас будет мебель для ванных комнат. Здесь этому материалу тоже нет равных в плане влагостойкости, и эколисты вполне могут стать экологичной заменой натуральному и искусственному камню.
Процесс производства
— Сергей, расскажите подробнее о процессе производства…
— В результате горячего прессования на станках мы получаем листовой материал полностью из вторичного пластика. Как уже говорилось, особенностью такого метода переработки в отличие от экструзии является цвет — он неоднородный, по фактуре напоминает натуральный камень. Можно пробовать самые разные эффекты, смешивать цвета, делать орнаменты. Каждая поверхность получается неповторимой, эксклюзивной.
За время работы мы успели поэкспериментировать: например, перенесли логотип через пакет (просто положили сверху сырья пакет и запекли), делали узоры из крышечек, добивались эффектов мрамора, звездного неба, запекали блестки и мишуру. Работа с цветом в процессе прессования листов — одновременно и преимущество, и недостаток: пластик нельзя окрасить, лист будет таким, какого цвета было сырье, и тут уже возникает проблема для серийного запуска, ведь каждая партия вторичного сырья даже от одних и тех же поставщиков может немного отличаться по оттенку. При этом его может и не быть в нужном количестве. Но в целом при выстраивании партнерства с ответственным производителем вторичной гранулы, думаем, вопрос будет решен.
— Какое сырье используете?
— Бытовой пластик от населения, который мы закупаем в пунктах приема, вторичную гранулу и дробленку. Используем ПЭНД, ПЭВД, реже — полипропилен.
Бытовой пластик (канистры, бутыли, крышки) сначала сортируем по цвету, затем измельчаем в крошку на шредере, и уже дробленый пластик запекаем под прессом. Естественно, при использовании гранулы или дробленки этап досортировки и дробления пропускается. Для увеличения производительности в настоящее время в большей степени используем вторичную гранулу.
— Как, собственно, протекает процесс прессования?
— Первым делом подготавливаем форму. Форма — это два стальных листа, между которыми размещается квадрат со стороной 110 см из профильной трубы нужного размера (1 см, 2 см). Листы обрабатываются литьевой термостойкой смазкой. В форму засыпается пластик: для листа толщиной 1 см понадобится 11 кг сырья, толщиной 2 см — 22 кг. Стальные листы с формой и пластиком помещаются в рабочее поле термопресса, разогретого до 180°C. Под давлением 3-5 т материал выдерживается 1-1,5 ч. За это время пластик подплавляется, смешивается и становится единым листом.
После запекания листу нужно остыть. Для того чтобы термопресс можно было использовать для изготовления следующего изделия, горячая форма перемещается в пресс без подогрева, и пластик находится там еще полтора часа, пока в горячем прессе запекается следующий лист — все должно работать как конвейер.
Но этого времени не хватает, чтобы пластик схватился, из формы его не вытащить, и к тому же при перемещении возможна деформация листа, поэтому для качественных листов нам приходится выдерживать пластик немного дольше под прессом. Таким образом, скорость процесса производства проседает. Если изначально при расчетах мы закладывали 6 листов в смену (12 часов), то по факту мы получаем, что на формирование одного качественного листа на действующем оборудовании уходит около 3 ч, и соответственно в смену можно сделать только 4 листа. Конечно, для полноценного производства это очень мало. Сейчас мы уже не успеваем закрывать заказы с той скоростью, с которой хотелось бы.
Перспективы развития
— Анна, как планируете развиваться дальше?
— Сейчас мы находимся в поиске нового оборудования и новых решений, так как действующие станки имеют очень маленькую производительность и больше подходят для просветительской деятельности (мастер-классов, единичных декоративных изделий). Но нам все-таки хочется развивать этот метод переработки в промышленных масштабах, с возможностью постепенного роста и наращивания объемов.
Пока из компаний, к которым мы обращались по поводу оборудования, ответила только одна. Сейчас мы ведем переговоры с предприятием «Ростполикрафт» по поводу разработки автоматизированной линии по прессованию эколистов, чтобы хоть как-то повысить производительность.
Они предложили разделить два процесса (плавление и прессование) на разные этапы. То есть сначала пластик размещается в печке, подплавляется, и в горячем состоянии форма перемещается на роликах в пресс с водяным охлаждением. Технологию прессования вторичного пластика таким образом мы видели у компании Madera Plastica (Индия). Также при изменении процесса перемещение форм от места к месту происходит полуавтоматически, что также положительно влияет на сокращение длительности процесса. Разделение этапов позволит создать конвейер и ускорит сам процесс: на подплавление пластика понадобится только 45-60 мин, прессование и охлаждение займут столько же времени. Другие плюсы нового решения: будет увеличен размер листов (2×1 м), а производительность увеличится до 20-24 листов в день. Рыночная стоимость квадратного метра листа в размере 3500-4000 рублей будет вполне конкурентоспособной и при этом выгодной для производителя.
— Планируете ли улучшать качественные характеристики листов?
— Да, над тактильными ощущениями и общим видом продукции тоже нужно поработать. Пока нам не удалось добиться глянцевого эффекта: не удается добиться взаимодействия полировочных материалов, паст и смазок с эколистами. А ведь глянцевая поверхность — один из ключевых критериев при покупке мебели населением. Также существует проблема неровностей, пузырей внутри листа.
Будем рады, если с нами свяжутся компании, которые могут помочь советом или делом, и в партнерстве мы сможем серийно получать экоизделия достойного
качества.
Беседовала Анна Виленс
Посмотреть в журнале