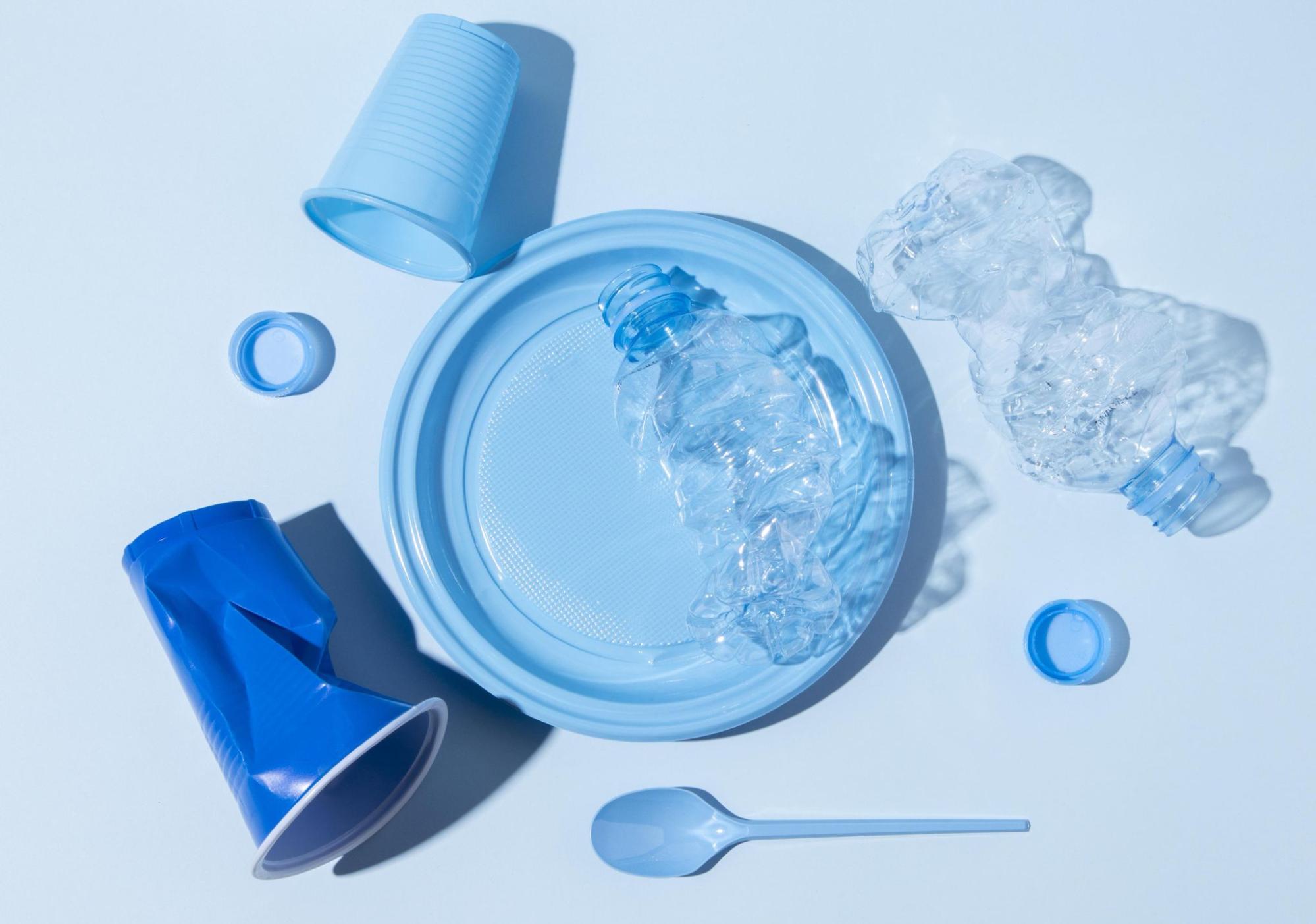
Новые направления переработки ПЭТ-отходов
Во всем мире динамично растет рынок изделий из ПЭТ, соответственно, увеличивается и объем отходов из полиэтилентерефталата. В своей новой статье эксперты журнала «Пластикс» анализируют различные варианты переработки данных отходов, позволяющие реализовать наиболее перспективные технологии для получения на их основе высоколиквидных материалов и изделий
Рынок ПЭТ-отходов
В 2016 году в мире выпущено 21,4 млн т ПЭТ-сырья для изготовления более 550 млрд бутылок, произведено 16 млн т полиэфирных/штапельных волокон и 36 млн т нитей [1, 3-4]. Однако при всем совершенстве современных технологий переработки образуется большое количество ПЭТ-отходов с различными характеристиками и степенью загрязненности. Только отходов ПЭТ-волокон и нитей по самым скромным расчетам накапливается в год около 2,5 млн т. Сбор ПЭТ-бутылок в мире в 2016 году превысил 11,2 млн т [2]. В России объем потребления ПЭТ в виде тары в 2016 году был рекордным и составил около 600 тыс. т. При этом в стране было произведено 534 тыс. т ПЭТ, экспорт составил 36 тыс. т, а импорт ― порядка 108 тыс. т.
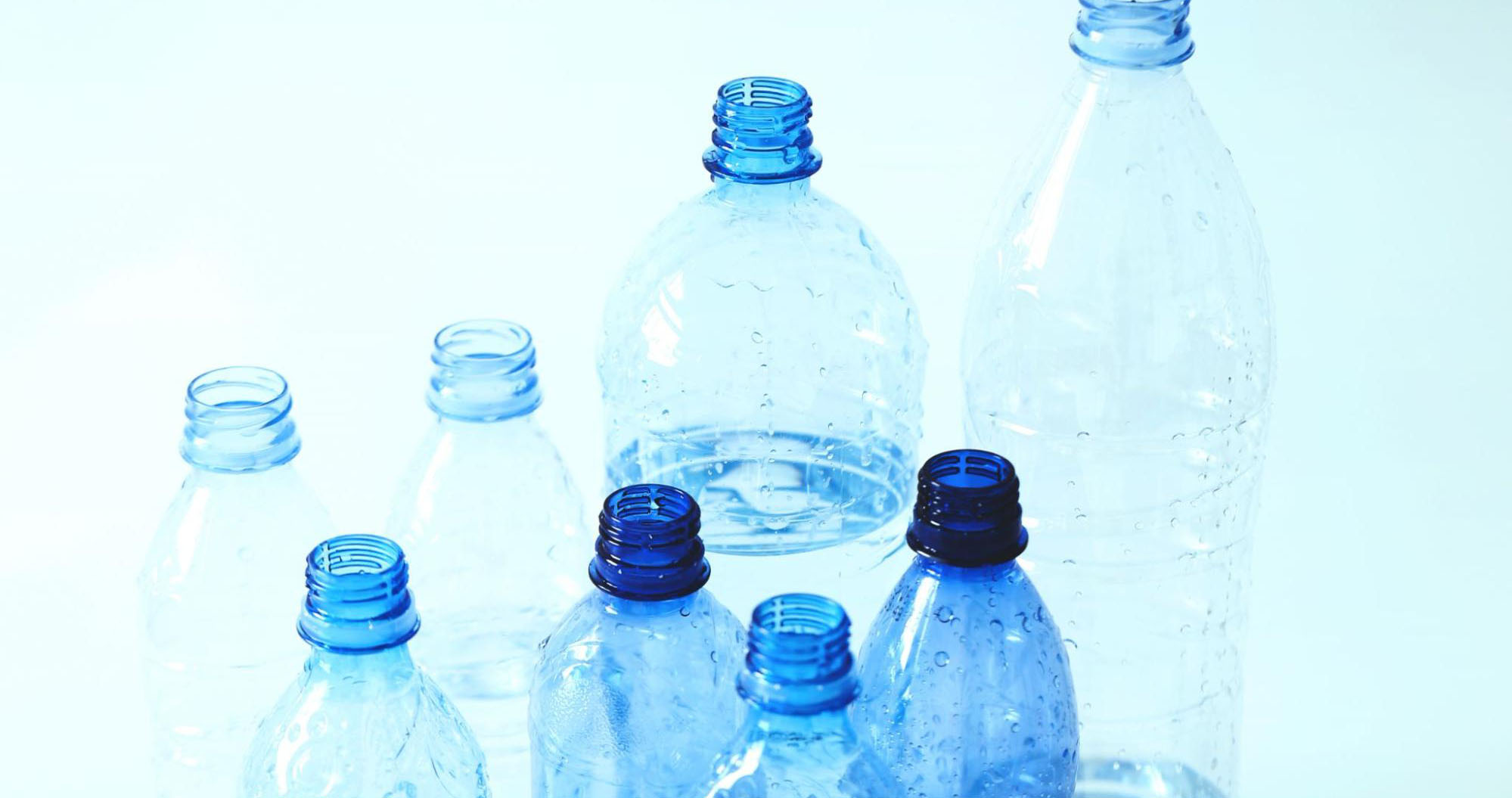
Классификация ПЭТ-отходов и некоторые процессы для их рациональной переработки описывались нами ранее [4-7]. Ввиду постоянного роста абсолютного количества ПЭТ-отходов, ужесточения требований к экономии энергии и органического сырья, а также проблем экологии вопросы оптимальной переработки изделий из полиэтилентерефталата требуют самых оперативных решений.
Закон призван ускорить внедрение раздельного сбора мусора, что позволит увеличить объемы собираемой в РФ ПЭТ-тары с сегодняшних 25% (в 2016 году было собрано 160 тыс. т ПЭТ- отходов) как минимум до 35-45%. Эта планируемая цифра меньше, чем в Китае (80%) и странах ЕС (55%), но больше, чем было до введения в России нового закона. В ближайшие четыре года в РФ будет собираться до 270 тыс. т ПЭТ- бутылок в год.
Заводы по переработке ПЭТ-бутылок в России
В России заметно увеличивается количество заводов, которые позволяют сократить количество пластиковых отходов и способствуют улучшению экологической ситуации. Они используют современные технологии, позволяющие перерабатывать большие объемы собранного пластика в флексы и другие полуфабрикаты для дальнейшего производства волокон, нитей и других изделий. С ростом числа таких заводов появляются и новые способы утилизации, что способствует созданию замкнутого цикла переработки отходов из ПЭТ.
Примеры таких заводов:
- Завод по переработке пластмасс «Пларус», TotalCycle, Завод «АРТЭКО»
Вторичная переработка ПЭТ-отходов в грубое штапельное волокно и нетканые материалы не является единственным и оптимальным решением для использования этого ценного сырья. В последнее время все чаще фирмы, перерабатывающие ПЭТ-бутылки в полупродукты для последующей переработки, останавливают свой процесс на выпуске чистой измельченной фракции ― флексах, не превращая их в гранулы.
Флексы ― тонкие пластинки размером 3-12 мм ― впоследствии прекрасно перерабатываются в экструдерах. Их единственный минус ― низкая насыпная плотность (300-400 кг/м3), которая ведет к удорожанию логистики данного материала. Однако поскольку скорость диффузии пропорциональна площади поперечного сечения, малые размеры флексов минимизируют расход энергии при их сушке, кристаллизации, отгонке легколетучих компонентов.
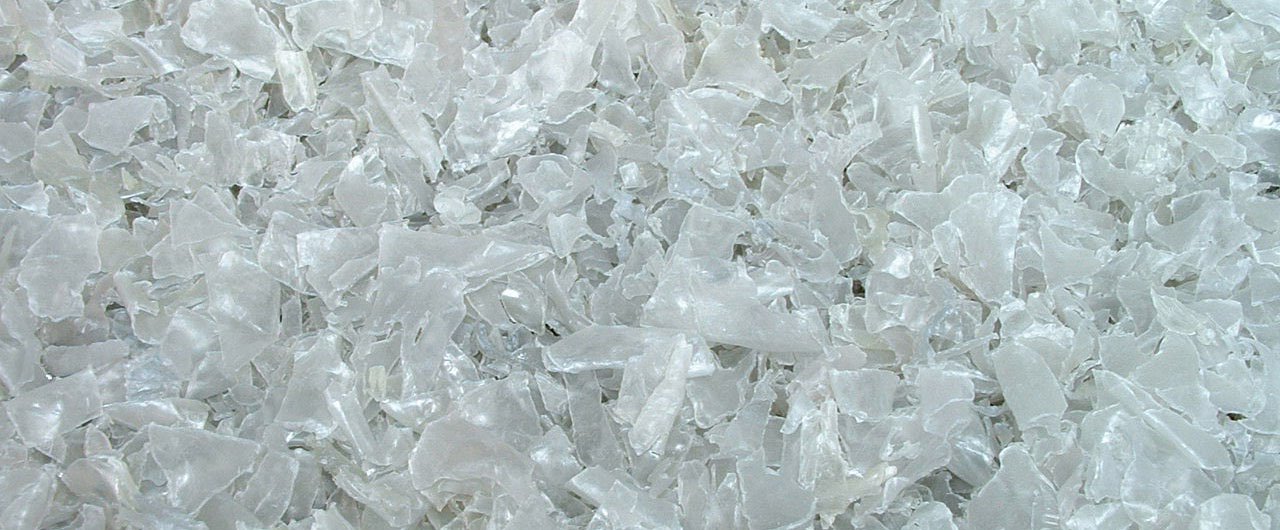
В процессе переработки ПЭТ оптимальная температура является критически важным параметром, влияющим на качество и стабильность получаемых материалов. Например, для экструзии ПЭТ-флексов требуется поддерживать строгий температурный режим, который позволяет удалять летучие вещества и контролировать вязкость расплава. В мультишнековых экструдерах температура переработки ПЭТ оптимизирована для достижения высокой однородности материала и минимизации гидролиза, что положительно сказывается на прочности и долговечности конечной продукции.
Производство волокон и нитей
В опубликованных ранее статьях были изложены основные принципы получения новой ПЭТ-тары с использованием отходов [5, 7]. В последнее время на рынке также появились новые технологии производства более качественных типов штапельного волокна и нитей из ПЭТ-флексов.
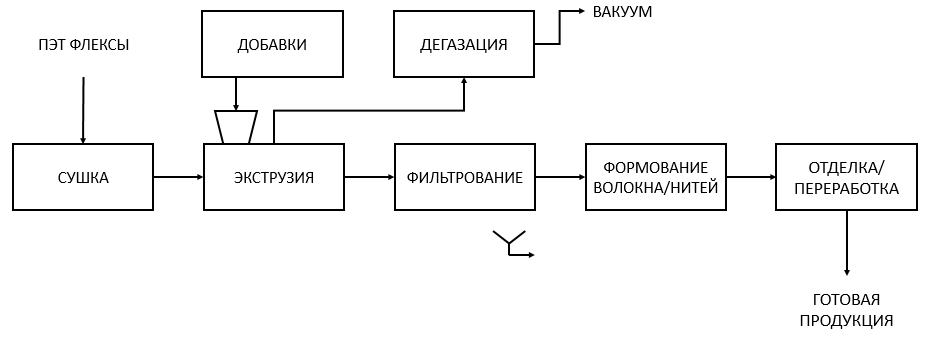
Рисунок 1. Схема получения ПЭТ-волокон и нитей из бутылочных отходов
Принципиальная схема таких процессов представлена на рис. 1. Она имеет некоторые особенности и различия для волокон и нитей. Так, при производстве волокон некоторые фирмы не используют сушку флексов, поскольку применяют двухшнековые и особенно мультишнековые экструдеры, обеспечивающие высокую поверхностью раздела фаз и эффективную дегазацию, минимизирующую гидролиз расплава. При выпуске же нитей сушка необходима. Комплектная установка VarioFil® R+ для получения полиэфирных POY-нитей (Pre Oriented Yarn ― предварительно ориентированные нити) из флексов, разработанная фирмами ВBEngineering и Oerlicon Barmag (ФРГ), имеет производительность до 11 т/сутки и позволяет получать продукцию с достаточно высокими физико-механическими показателями. Нити формуются с классическими скоростями намотки (2500-3400 м/мин.) с использованием боковой обдувки на 4 позициях формования (10 нитей на позицию).
Независимые исследования, проведенные ВНИИСВ (Тверь), изготовленных на установке VarioFil® R+ POY-нитей и полученных из них DTY- текстурированных нитей (Fully Drawn Yarn ― полностью вытянутые (ориентированные) нити) показали, что их свойства мало отличаются от подобной же продукции, произведенной из первичного ПЭТ. Например, DTY-нить 16,9 текс имела разрывную нагрузку 0,72 кгс, удельную разрывную нагрузку 42 г/текс, удлинение при разрыве 14,6%, а при низких коэффициентах — вариации этих показателей.
В табл. 1 приведены рекомендуемые характеристики флексов для производства пищевых бутылок, нитей и волокон. Свойства эти весьма схожи, причем особенно стоить отметить, что повышенная контаминация ПВХ- включениями пагубно сказывается на качестве флексов. Естественно, по мере развития программы раздельного сбора отходов, минимизирующей возможность загрязнения ПЭТ-тары по сравнению с поставляемой сегодня на перерабатывающие заводы «полигонной» бутылкой, на российском рынке будут появляться в промышленном объеме флексы более высокого качества.
Показатель | Бутылка | Нить | Волокно |
Характеристическая вязкость IV, дл/г | ≤0,8 | ≤0,72-0,84 | ≤0,75-0,84 |
Содержание полиолефинов, частей на миллион | 0-10 | 0-20 | 0-50 |
Содержание бумаги, частей на миллион | 0-10 | 0-10 | Σ3+4+5=100 |
Содержание металлов, частей на миллион | 0-10 | 0-10 | Σ3+4+5=100 |
Содержание органических веществ, частей на миллион | 0-10 | 0-10 | Σ3+4+5=100 |
Содержание ПВХ, частей на миллион | 0-20 | 0-10 | 0-20 |
Относительный уровень кислотности (pH) | 7 | 7 | 8,5 макс. |
Конечное содержание влаги, % | 0,6-0,7 | 0,6-0,7 | 1 |
Содержание флексов размером 5- 8 мм, % | 95 | 94 | 95 (4-14 мм) |
Содержание мелких фракций (≤2 мм), % | ≤1 | ≤0,1 | ≤1 |
Таблица 1. Рекомендуемые характеристики флексов для производства пищевых бутылок, нитей и волокон
Вполне возможно появление на рынке технологий производства из ПЭТ- флексов некоторых типов технических нитей ― в первую очередь для производства геосеток для армирования верхнего слоя дорожного полотна [6]. Разумеется, даже после повышения вязкости флексов (с IV 0,75-0,84 до 0,95-1,0) методом твердофазной дополиконденсации (скорость реакции для флексов выше, чем для гранул) они не смогут конкурировать по своим физико- механическим показателям (прежде всего по прочности) с используемыми для этой цели высокомодульными нитями НМ (удельная разрывная нагрузка 820 мН/текс) из первичного ПЭТ, поскольку флексы представляют собой сополимер с довольно широким молекулярно-массовым распределением. Однако, требуемая прочность собственно геосетки для некоторых сфер применения может быть достигнута за счет увеличения титра (толщины) нити. При этом могут использоваться и цветные флексы, поскольку на геосетки затем наносится дисперсия ПВХ.
При выпуске некоторых «неответственных» типов полиэфирных волокон возможно использование в производстве агломерированных собственных отходов волокон путем их ввода в финишный реактор поликонденсации (при прямом формовании) или в экструдер (при экструзионном формовании).
Основными проблемами осуществления таких процессов является необходимость удаления из отходов волокна замасливателя и низкая вязкость вводимого агломерата волокнистых отходов.
Смесь флексов и агломерата
Весьма перспективной является технология ввода в расплав первичного ПЭТ после реактора поликонденсации смеси расплавов: ПЭТ-флексов с высокой вязкостью и ПЭТ-агломерата отходов штапельного волокна низкой вязкости с их последующим смешением (статические гомогенизаторы) с основным потоком первичного расплава и подачей на прямое формование штапельного волокна.
Совершенно очевидно, что вводимая смесь полимеров с разной вязкостью расплава обладает широким молекулярно-массовым распределением, но тем не менее она хорошо формуется (в смеси с наличием первичного расплава из реактора поликонденсации) и позволяет получать некоторые виды волокна вполне удовлетворительного качества.
Решение, допускающее при производстве штапельного волокна ввод помимо флексов (IV 0,75-0,84) до 20% агломерированных волокнистых отходов (IV 0,6 -0,64), было разработано и апробировано российскими и немецкими специалистами в рамках проработки проекта Ивановского полиэфирного комплекса с подбором передовых технологий и оборудования. Гранулы, полученные из смеси 80% флексов и 20% агломерата, произведенного по технологии фирмы Herbold (Германия), были успешно переработаны на опытном штапельном агрегате фирмы Truetschzler (Германия) в волокно толщиной 7 денье с показателями, практически не отличающимися от таковых для волокна из первичных ПЭТ-гранул. Незначительное ухудшение показателя цветности волокна может быть компенсировано введением оптических отбеливателей. Принципиальная схема данной технологии приведена на рис. 2.
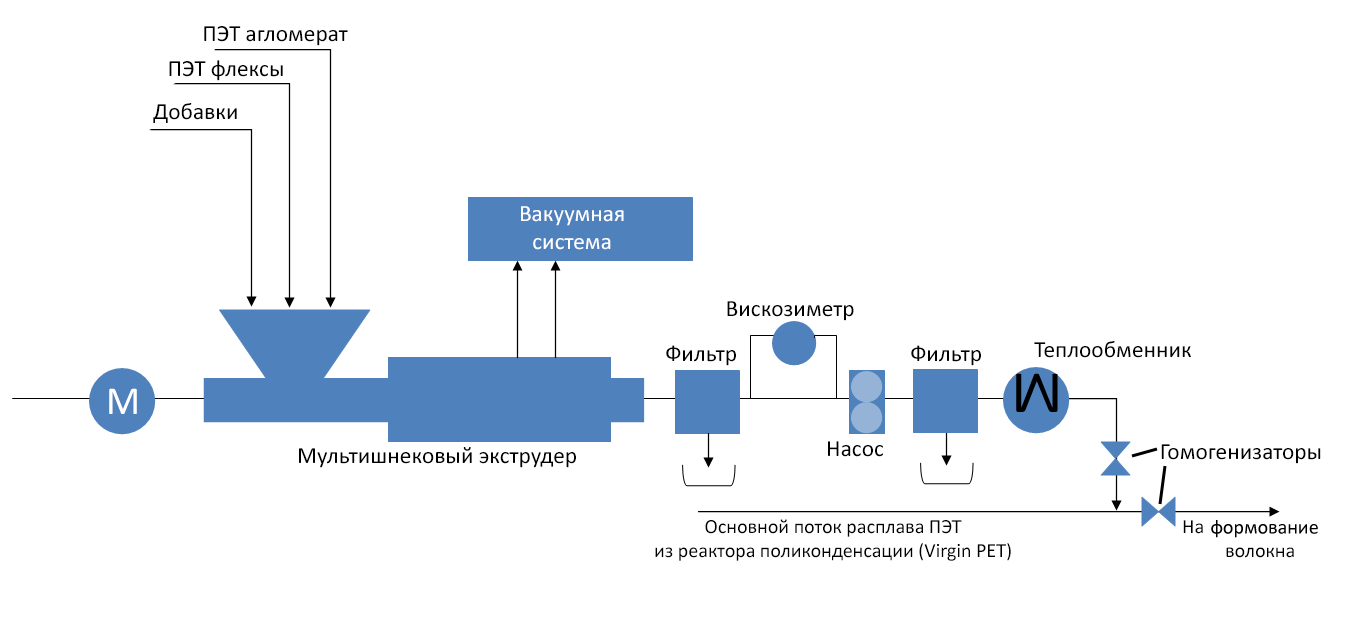
Рисунок 2. Схема получения волокна из смеси ПЭТ-флексов и ПЭТ- агломерата
На практике ПЭТ-флексы и агломерат ПЭТ-волокна будут вводиться в экструдер. Туда же могут подаваться и малые количества добавок (мастербатч красителя, диоксид титана, антипирены). В качестве последних все чаще используются полифосфонаты, не высвобождающиеся из полимерной матрицы, нетоксичные и обеспечивающие время угасания пламени в некоторых полиэфирных тканях менее 1 с [9].
Экструзия (предпочтительнее мультишнековые экструдеры) с мощной зоной дегазации и последующая фильтрация (чаще двухстадийная до получения частиц размером 20 мкм) обеспечивают деконтаминацию расплава удалением летучих и твердых загрязнений и его максимальную гомогенизацию.
При вводе агломерированных волокнистых отходов одной из важнейших задач является отгонка под вакуумом (под давлением до 0,001 мбар) содержащейся в них прядильной препарации, наличие которой в расплаве нарушает процесс формования волокна. Тонкая фильтрация расплава ПЭТ от посторонних примесей позволяет устранить все твердые включения и обеспечить тем самым длительный срок службы (для столь специфичного полимера) фильерных комплектов. Для этой цели используется каскад двух фильтров (с ячейками 40 мкм и 20 мкм) с обратной промывкой фильтрующих поверхностей расплавом. Система дегазации экструдера должна обеспечивать постоянную работоспособность и безопасное удаление из процесса улавливаемых летучих компонентов.
Основными параметрами, оказывающими существенное влияние на эффективность переработки отходов по приведенной выше схеме и стабильность свойств (прежде всего вязкости) расплава полимера, подаваемого на формование, являются:
- температурный режим;
- глубина вакуума;
- пропорция вводимых в экструдер низко- и высоковязкого компонентов;
- уровень ввода этиленгликоля для снижения или выравнивания вязкости (опция), гибко регулируемой при помощи встроенного вискозиметра расплава.
Наилучшие показатели качества волокна, изготовленного по приведенной на рис. 2 схеме, были достигнуты при переработке вторичного ПЭТ на оборудовании фирмы Gneuss (Германия): экструдер MRS с мультишнековой зоной дегазации и вакуумной системой VAC, самоочищающиеся фильтры расплава с обратной промывкой типа RSFgenius и вискозиметр VIS, интегрированные с оригинальной системой управления.
Оборудование и технология фирмы Gneuss будут использованы при реализации проекта Ивановского полиэфирного комплекса на базе двух комплектных линий по переработке ПЭТ-отходов мощностью до 50 т/сутки каждая.
Выпуск нетканых материалов и преформ
Из ПЭТ-флексов могут производиться специальные нетканые материалы для самых различных областей применения. Перспективным продуктом является тепло- и звукоизоляционный материал толщиной от 20 до 200 мм плотностью 15 кг/м3 и с теплопроводностью 0,041 Вт/м∙К. [10].
Весьма эффективным является использование полиэфирных волокон из вторичного ПЭТ при обустройстве и восстановлении битумных и цементно- битумных дорожных покрытий, так как данный тип волокна легко смешивается с горячим битумом и бетоном, придавая последним повышенную прочность и долговечность. Результат применения ― предупреждение раннего трещинообразования дорожного покрытия, повышение его устойчивости к высоким и пониженным температурам, снижение порога «усталости» материалов, повышение гибкости покрытия и его устойчивости к просачиванию влаги, а следовательно, и общей износостойкости, продление срока эксплуатации дорожного полотна. Эти эффекты достигаются при дозировке от 1,2 до 3,5 кг волокна на 1 т битумной смеси.
Есть новинки и в производстве преформ. Фирма EREMA (Германия) объявила о разработке новой технологии и соответствующего оборудования для выпуска преформ не из гранул, а из флексов. В содружестве с SIPA компания EREMA представила новую установку, основанную на методе литья с использованием инъекционного сжатия. Способ позволяет снизить давление и потери вязкости при изготовлении преформ и сократить содержание в них ацетальдегида. Промышленное тестирование первой машины намечено на вторую половину 2017 года [11].
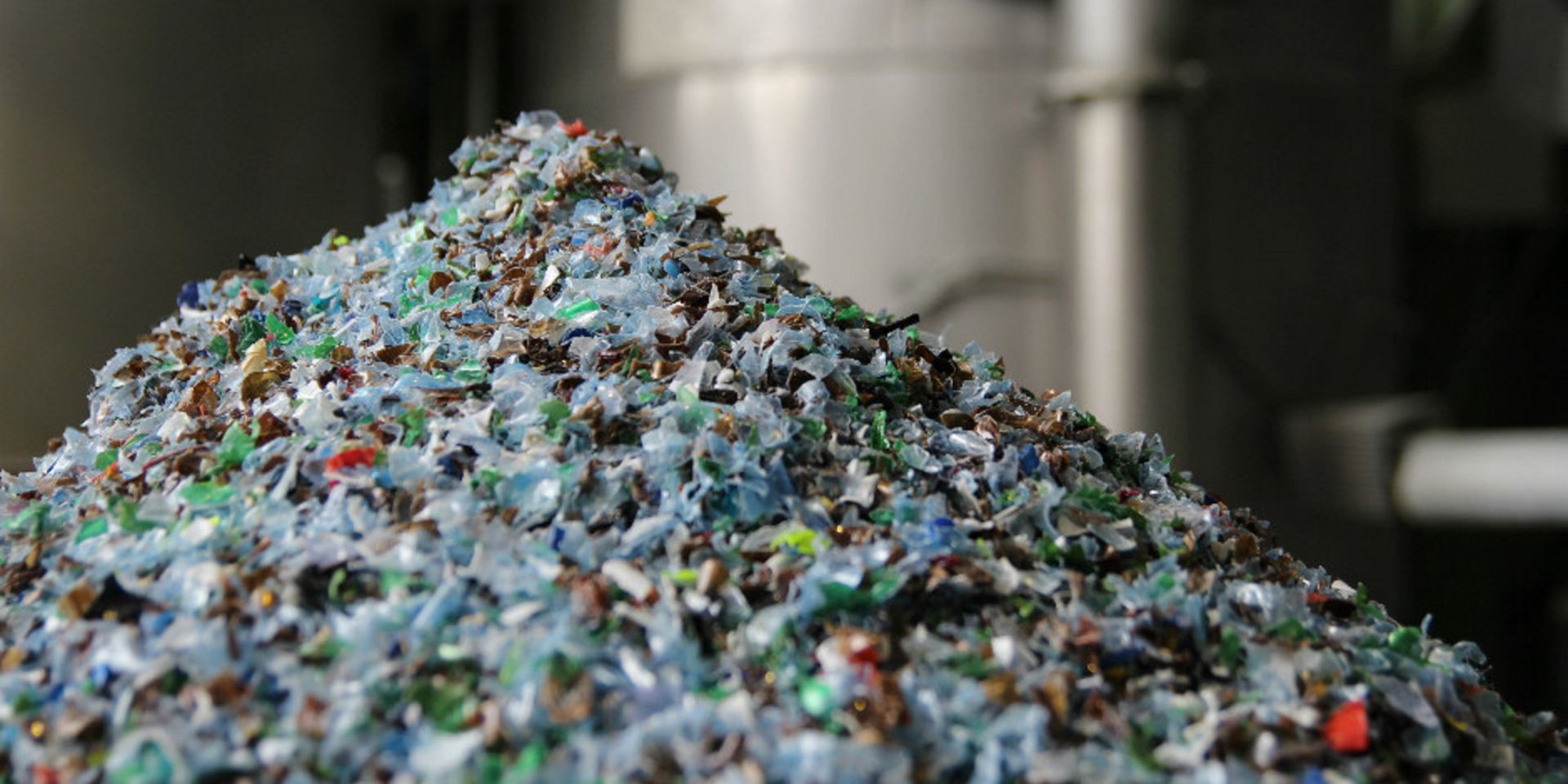
ПЭТ-рециклят может использоваться также в смесях с другими полимерами. Так, смеси ПЭТ с полиарилатами применяются для выпуска упаковки для косметики благодаря более высокой прочности (71 МПа) по сравнению с ПЭТ (около 50 МПа). Во многих случаях смеси ПЭТ являются частично смесями, а частично сополимерами, что объясняется возможностью протекания реакции трансэтерификации при экструзии. Такой эффект исследован и описан для смесей ПЭТ и ПБТ [12]. Это характерно и для смесей на основе флексов ПЭТ и ПЭН (полиэтиленнафталат), существенно более дешевых, чем чистый ПЭН, но при этом обладающих почти такими же высокими барьерными свойствами, как у ПЭН, и более высокой по сравнению с ПЭТ термостойкостью [13]. Такие материалы перспективны для изготовления упаковки элитных продуктов, высокочувствительных к окислению.
Также весьма перспективно применение нанокомпозитов на основе вторичного ПЭТ и слоистых алюмосиликатов, обладающих повышенной огнестойкостью и гораздо более высокими по сравнению с первичным ПЭТ барьерными свойствами по отношению к O2 и CO2 [14]. Еще более эффективным процессом, чем смешение этих компонентов в расплаве, является полимеризация в реакторе, когда наноглина диспергируется в мономере или полупродукте, а затем в процессе реакции полимеризации — в полимере.
Известна успешная коммерциализация такой технологии для полиамидов и полиэфиров. Разработка нанокомпозитов на основе ПЭТ ― актуальное направление, востребованное в секторе производства различной техники и упаковки.
С точки зрения экологии увеличение объемов сбора и переработки ПЭТ отходов уменьшает загрязнение окружающей среды. Следует отметить, что невыбранная с полигонов ПЭТ-бутылка может безопасно сжигаться в общей массе отходов на мусороперерабатывающих заводах (теплотворная способность ПЭТ составляет 22700 кДж/кг), поскольку она практически не дает при этом никаких токсичных продуктов [16].
Технологии получения новых высоколиквидных материалов и изделий (особенно с длительным жизненным циклом) из отходов ПЭТ стимулируют увеличение объемов вторичной переработки этого полимера, способствуют экономии энергии и рациональному использованию ценного углеводородного сырья.
Литература
1. McGeough H., Mackenzie PCI GROUP. «Обзор мирового рынка ПЭТ», доклад на конференции «ПЭТФ-2017». — Москва. 16 февраля 2017.
2. McGeough H., Mackenzie PCI GROUP. «Обзор мирового рынка вторичного ПЭТ», доклад на конференции «Вторичная переработка полимеров — 2017». — Москва. 17 февраля 2017.
3. Керницкий В.И., АРПЭТ. «Российский ПЭТ», доклад на конференции «ПЭТФ-2017». — Москва. 16 февраля 2017.
4. Керницкий В.И., Жир Н.А., Микитаев А.К. ПЭТ: приказано выжить // Пластикс. — 2015. — №12 (152). — С. 32-38.
5. Керницкий В.И., Жир Н.А. Отходы полиэтилентерефталата (ПЭТ) и перспективные направления их переработки // Известия Кабардино-Балкарского государственного университета. — Т. V, №6. — Нальчик, 2015. — С. 47-50.
6. Керницкий В.И., Микитаев А.К. Производство и переработка полиэтилентерефталата. — М.: изд. РХТУ им. Д.И. Менделеева, 2015. — 282 с.
7. Керницкий В.И., Жир Н.А. Переработка отходов полиэтилентерефталата (ПЭТ) // Полимерные материалы. — 2014. — №8. — С. 12-21.
8. Федеральный закон №458-ФЗ «О внесении изменений в Федеральный закон «Об отходах производства и потребления», отдельные законодательные акты Российской Федерации и признании утратившими силу отдельных законодательных актов (положений законодательных актов) Российской Федерации» // СПС «КонсультантПлюс».
9. Ленс Ж.П. Полифосфонаты: безопасная огнезащита // Пластикс. — 2015. — №12 (152). — С. 19-23.
10. Ziegler J.H., Allgemeine bauaufsichtliche Zulassung fuer Polyestervlies- Dammstoff, Technische Textilien 2/2013. S. 70.
11. Vioss Ch. «Поточное производство пищевых пластиковых бутылок из ПЭТ-хлопьев», доклад на конференции «Вторичная переработка полимеров — 2017». — Москва, 17 февраля 2016.
12. Микитаев М.А., Козлов Г.В., Микитаев А.К. Влияние реакции трансэтерификации в смесях полиэтилентерефталат/полибутилентерефталат на их прочность // Известия Кабардино-Балкарского государственного университета. — Т. V, №6. — Нальчик, 2015. — C. 14-17.
13. Зелке С., Кутлер Д., Хернандес Р. Пластиковая упаковка / Пер. с англ. 2-го изд. Под ред. Загорского А.Л., Дмитрикова П.А. — СПб.: ЦОП «Профессия», 2011. — 560с.
14. Беданоков А.Ю., Бештоев Б.З., Микитаев М.А., Микитаев А.К., Сазонов В.В. Полиэтилентерефталат: новые направления рециклинга // Пластические массы. — 2009. — №6. — С. 18-21.
15. Бухарова Е.А. «Сорбционные материалы на основе отходов полиэтилентерефталата и соединений графита для очистки сточных вод», диссертация на соискание ученой степени, к.т.н., Саратовский государственный технический университет имени Юрия Гагарина. — Саратов, 2015.
16. Katami T., Yasuhara A., Shibamoto T. Formation of PCDDs, PCDFs and Coplanar PCBs from Polyvinil Chloride during Combustion in an Incinerator// Environ. Sci. Technol. 2002. No. 36. P. 1320-1324.