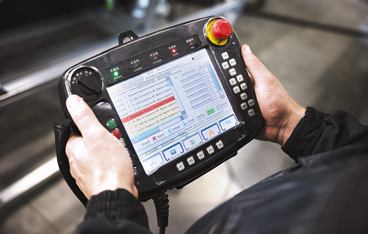
24.01.2024
Диагностика полимерного оборудования
Российский поставщик оборудования для переработки полимеров «Интерпласт» (Interplast, Вологда) начал выполнять диагностику технического состояния ТПА, экструдеров, экструзионно-выдувных машин и вспомогательного оборудования. Эксперты разработали специальную программу, закупили инструмент для проведения сервисных работ. Данная мера поможет переработчикам пластмасс внедрить механизм предупреждения аварийных ситуаций и добиться сокращения затрат.
Предупрежден — значит вооружен
Специалисты компании «Интерпласт» утверждают, что, независимо от отраслевой принадлежности и масштабности полимерных предприятий, многие производители не проводят техническое обслуживание оборудования и не располагают собственной сервисной службой. Это, безусловно, сопряжено с высоким риском непредвиденных финансовых потерь по причине выхода оборудования из строя вследствие поломки.
Один из эффективных способов решения данной проблемы — обратиться к поставщику, который специализируется на данном виде услуг, и осуществить диагностику парка машин. Процедура эффективна при выполнении таких задач, как определение фактической производительности, степени износа и запаса прочности оборудования, выявления дефектов узлов и агрегатов, оценка возможности ремонта или модернизации.
Александр Павлов, руководитель инженерного отдела «Интерпласт», отмечает: «В промышленности реальность такова: производители готовы нести серьезные денежные расходы на аварийный ремонт, замену деталей и узлов, но не готовы платить в десятки раз меньше за диагностику оборудования. Сама по себе диагностическая проверка дает информацию о текущем техническом состоянии линий и систем. Располагая такими данными, предприятие может оперативно реагировать на те или иные проблемы, рассчитывать вероятность отказа установок, а также грамотно определять потребность в финансировании мероприятий для поддержания работоспособности и техобслуживанию технологического парка».
Диагностика — это работающий механизм предупреждения аварийных ситуаций и сокращения ненужных расходов. Однако следует учитывать, что неисправное оборудование не в состоянии обеспечивать оптимальный уровень производительности и качества продукции. Так, один из клиентов компании «Интерпласт» столкнулся с резким падением производительности экструзионной линии на 25%. Причина была проста, но визуально дефект был не заметен: зазор между шнеком и цилиндром увеличился всего на 0,1 мм. Подобный вид износа невозможно выявить без специального инструмента, а между тем на предприятии произошел серьезный срыв производственных планов.
Два этапа диагностирования
Диагностирование включает следующие основные этапы:
— получение информации о техническом состоянии оборудования;
— обработка и анализ полученных данных.
Первый этап заключается в оценке внешнего вида, степени изношенности деталей и узлов, следов утечек рабочих жидкостей, а также в запуске оборудования и проверке его работы, измерении рабочих параметров и тестировании основных систем. Второй — в оформлении дефектной ведомости на каждый вид оборудования с указанием выявленных неисправностей, деталей и узлов, требующих ремонта или замены.
На одном из заводов в Якутии сотрудниками компании «Интерпласт» была проведена комплексная диагностика линии по производству топливных канистр с крышками. В результате было выявлено свыше 45 видов неисправностей, а самые неутешительные показатели состояния были определены для термопластавтомата и экструзионно-выдувной машины. К примеру, на ТПА не работала система автоматической смазки коленно-рычажного механизма из-за неисправного автоматического выключателя. Система смазки КРМ важна, но ее выход из строя легко не заметить, так как ТПА продолжит функционировать. Вместе с дефектной ведомостью клиенту были переданы замечания, перечень запчастей и приоритетный порядок ремонтных работ, а также список оборудования для автоматизации технологических процессов. Производство работало 10 лет без должного технического обслуживания, поэтому вернуть оборудование к паспортным характеристикам уже невозможно.
Когда предприятие занимается только изготовлением продукции, по сути, оборудование работает до момента отказа: у производителя нет графика планово-предупредительных ремонтов, нет представления о текущем техническом состоянии, о том, какие детали и узлы подлежат периодической замене или обслуживанию. В таком случае крайне необходима диагностика, позволяющая выявить проблемные места и устранить их еще до того, как оборудование сломается и производство встанет.
«Немногие компании оказывают такую услугу. Мы дополнительно предлагаем поставку необходимых запчастей и выполнение ремонтных работ. А также направляем письменные рекомендации, которые могут содержать, в частности, назначения по устранению неисправностей или информацию по необходимому обслуживанию», — заключает Александр Павлов.
Посмотреть в журнале
Предупрежден — значит вооружен
Специалисты компании «Интерпласт» утверждают, что, независимо от отраслевой принадлежности и масштабности полимерных предприятий, многие производители не проводят техническое обслуживание оборудования и не располагают собственной сервисной службой. Это, безусловно, сопряжено с высоким риском непредвиденных финансовых потерь по причине выхода оборудования из строя вследствие поломки.
Один из эффективных способов решения данной проблемы — обратиться к поставщику, который специализируется на данном виде услуг, и осуществить диагностику парка машин. Процедура эффективна при выполнении таких задач, как определение фактической производительности, степени износа и запаса прочности оборудования, выявления дефектов узлов и агрегатов, оценка возможности ремонта или модернизации.
Александр Павлов, руководитель инженерного отдела «Интерпласт», отмечает: «В промышленности реальность такова: производители готовы нести серьезные денежные расходы на аварийный ремонт, замену деталей и узлов, но не готовы платить в десятки раз меньше за диагностику оборудования. Сама по себе диагностическая проверка дает информацию о текущем техническом состоянии линий и систем. Располагая такими данными, предприятие может оперативно реагировать на те или иные проблемы, рассчитывать вероятность отказа установок, а также грамотно определять потребность в финансировании мероприятий для поддержания работоспособности и техобслуживанию технологического парка».
Диагностика — это работающий механизм предупреждения аварийных ситуаций и сокращения ненужных расходов. Однако следует учитывать, что неисправное оборудование не в состоянии обеспечивать оптимальный уровень производительности и качества продукции. Так, один из клиентов компании «Интерпласт» столкнулся с резким падением производительности экструзионной линии на 25%. Причина была проста, но визуально дефект был не заметен: зазор между шнеком и цилиндром увеличился всего на 0,1 мм. Подобный вид износа невозможно выявить без специального инструмента, а между тем на предприятии произошел серьезный срыв производственных планов.
Два этапа диагностирования
Диагностирование включает следующие основные этапы:
— получение информации о техническом состоянии оборудования;
— обработка и анализ полученных данных.
Первый этап заключается в оценке внешнего вида, степени изношенности деталей и узлов, следов утечек рабочих жидкостей, а также в запуске оборудования и проверке его работы, измерении рабочих параметров и тестировании основных систем. Второй — в оформлении дефектной ведомости на каждый вид оборудования с указанием выявленных неисправностей, деталей и узлов, требующих ремонта или замены.
На одном из заводов в Якутии сотрудниками компании «Интерпласт» была проведена комплексная диагностика линии по производству топливных канистр с крышками. В результате было выявлено свыше 45 видов неисправностей, а самые неутешительные показатели состояния были определены для термопластавтомата и экструзионно-выдувной машины. К примеру, на ТПА не работала система автоматической смазки коленно-рычажного механизма из-за неисправного автоматического выключателя. Система смазки КРМ важна, но ее выход из строя легко не заметить, так как ТПА продолжит функционировать. Вместе с дефектной ведомостью клиенту были переданы замечания, перечень запчастей и приоритетный порядок ремонтных работ, а также список оборудования для автоматизации технологических процессов. Производство работало 10 лет без должного технического обслуживания, поэтому вернуть оборудование к паспортным характеристикам уже невозможно.
Когда предприятие занимается только изготовлением продукции, по сути, оборудование работает до момента отказа: у производителя нет графика планово-предупредительных ремонтов, нет представления о текущем техническом состоянии, о том, какие детали и узлы подлежат периодической замене или обслуживанию. В таком случае крайне необходима диагностика, позволяющая выявить проблемные места и устранить их еще до того, как оборудование сломается и производство встанет.
«Немногие компании оказывают такую услугу. Мы дополнительно предлагаем поставку необходимых запчастей и выполнение ремонтных работ. А также направляем письменные рекомендации, которые могут содержать, в частности, назначения по устранению неисправностей или информацию по необходимому обслуживанию», — заключает Александр Павлов.
Посмотреть в журнале